Proster articles - sources of professional knowledge
Industry knowledge compiled by specialists for specialists. Benefit from the experience of our experts.
William Edwards Deming
- quality guru
William Edwards Deming is referred to as a quality guru because he was one of the first, in the 1950s, to propose a modern approach to product quality by using staff management, planning, product design and process monitoring. Dr. Deming believed that 94% of all quality problems are the fault of management, which must engage in quality management and quality assurance. However, management should remember that decisions on these matters should be made together with employees.
Dr. Deming was a strong opponent of control and an opponent of American management methods such as management by objectives or management by results, and often criticised them. During his years of work, he has developed his own management methods to develop quality by changing the overall approach to managing human resources, material resources and production.
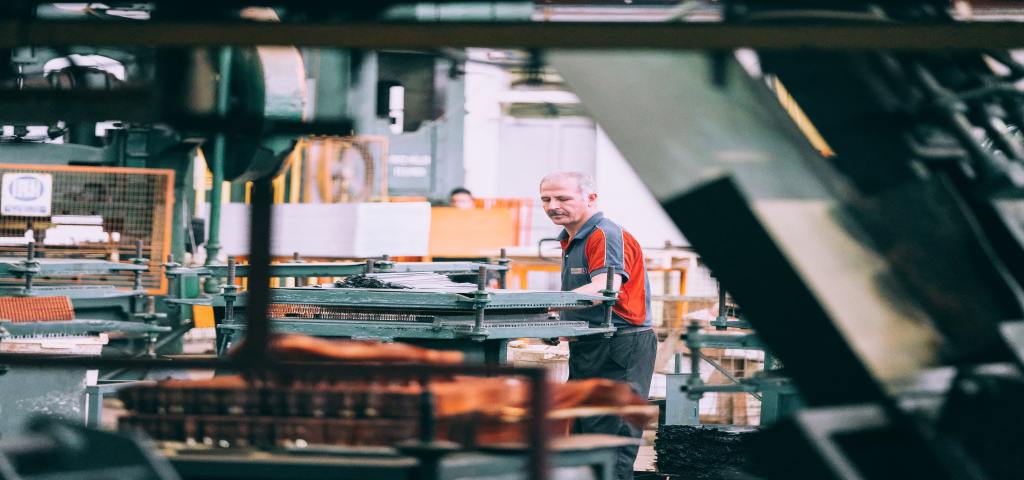
Among the management methods mentioned, he formulated theses, in the form of 14 points, called “Fourteen Points of Management System Transformation,” which management should follow in order to significantly improve business or organisational efficiency.
These points read as follows:
- Create constancy of purpose toward product and service improvement to become competitive and stay in business and provide jobs.
- Adopt a new philosophy. We are in a new economic era. Western executives must awaken to this challenge, must learn their responsibilities and take leadership for change.
- Abandon dependence on inspections to achieve quality. Eliminate the need for mass inspection by building quality into the product first.
- End the practice of rewarding companies based on price. Instead of that, minimise the total cost. Move toward a single supplier for each item, on a long-term partnerships of loyalty and trust.
- Improve the production and service system continuously, in order to improve quality and efficiency, and thus constantly reduce costs.
- Initiate on-the-job training.
- Leadership Institute. The goal of surveillance should be to help people, machines, and gadgets do a better job. Management supervision needs an overhaul, as does supervision of production workers.
- Drive out fear so that everyone can work effectively for the company.
- Break down barriers between departments. People from research, design, sales and production must work as a team to anticipate production and usage problems that may occur with a product or service.
- Eliminate slogans, admonitions and objectives for the workforce by asking for zero faults and new levels of productivity. Such exhortations only create hostile relations, since most of the causes of poor quality and productivity belong to the system and therefore lie beyond the reach of the workforce.
- Eliminate labour standards (quotas) on the factory floor. Replace them with leadership.
Eliminate management by objectives. Eliminate management by numbers, numerical targets. Replace with leadership. - Remove barriers that deprive the hourly worker of the right to pride in the work they have done. The responsibility of supervisors must be changed from mere numbers to quality.
Remove the barriers that deprive people in management and engineering positions of the right to pride of workmanship. This means, among other things, the abolition of annual or merit assessment and management by targets. - Introduce a vigorous programme of education and self-improvement.
- Involve everyone in the company in the work of achieving the transformation. Transformation is everyone’s responsibility.
On the basis of:
„Dr. Deming – The American Who Taught the Japanese About Quality” – by Rafael Aguayo.