Proster articles - sources of professional knowledge
Industry knowledge compiled by specialists for specialists. Benefit from the experience of our experts.
About the language of PackML
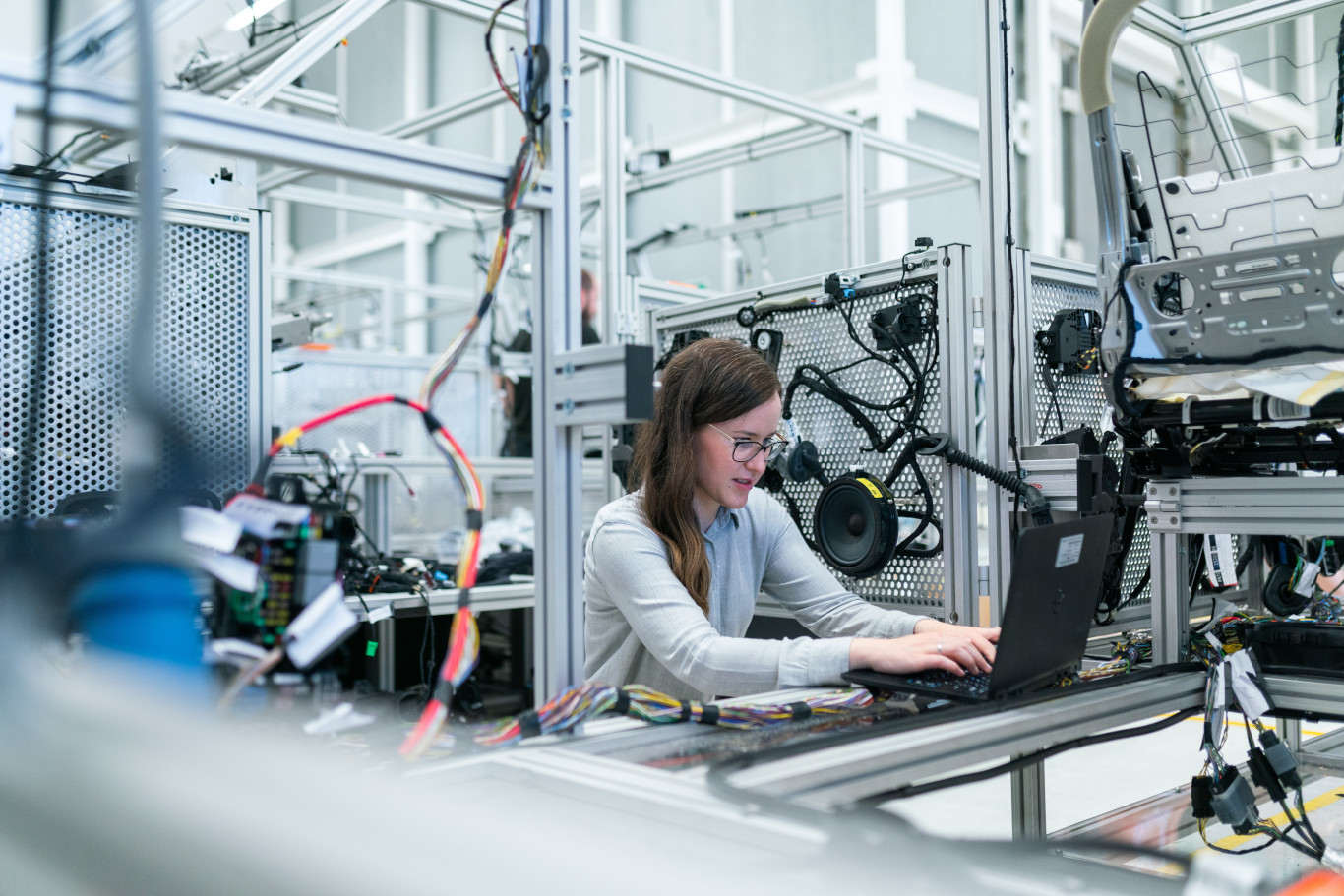
The Fourth Industrial Revolution is forcing modern manufacturing plants to efficiently collect significant amounts of data and respond flexibly to rapidly changing market needs. An example of such changes is an increase in demand for certain products, or for producing them in a certain way. For this to be possible, it is necessary for entrepreneurs to open up to broadly modernizing their production processes.
The period of the last two years has shown conclusively how important it is to ensure a stable supply chain at every stage of the chain. COVID-19 pandemic, earthquakes, floods, hurricanes… All of these hard-to-predict circumstances have affected and continue to affect the global economy. Most of the world’s markets are based on mass-market-directed products that need to be manufactured, packaged, stored and delivered to their destinations quickly and continuously. One of a wide range of solutions dedicated to manufacturing plants is to ensure that machines function in a technical standard – the so-called PACKML (Packaging Machine Language). The author of this solution is the Organization for Machine Automation and Control (OMAC) i.e. a global organisation that supports the automation of machinery and production operational needs. The standard was originally developed for packaging machines, but over time its use has expanded. Work on the standard began in 2000 to release it in 2008, as a component of the ISA-S88 standard – ISA-TR88.00.02. The PackML standard consists of three main elements; modes of operation, state model and Packtags.
The primary task of PACKML is to enable seamless communication and cooperation between those working on the production line: cartoners, dispensers, palletisers, labelers, dispensers, cappers. Each of these machines uses components from different suppliers, industrial computers, HMI screens. Each is also programmed differently and has different visuals. This variation makes it necessary for the services operating the machines to approach them individually and learn how to operate a particular machine from scratch each time. Production data collection and processing are also hampered. Also, on the side of the machine manufacturer (which has a ready-made control system), there is the problem of the end user, who may expect to work on a different, more familiar system. Everything contributes to longer deployment times, generates higher costs and makes it more difficult for maintenance services to diagnose the machine later. The answer to these problems is precisely PACKML, which ensures the functional cooperation and environmental consistency of the various machines working in the production hall. It greatly facilitates horizontal integration – of machines relative to each other, within a production line, as well as vertical integration – of a production line with a superordinate system (MES, SCADA, Historian) to calculate key production indicators (KPIs) such as OEE (Overall Equipment Effectiveness). This indicator shows how much good-quality products a machine can produce after subtracting wasted time (due to downtime and slower-than-expected work rates) and defective products.
Zalety wdrożenia standardu PACKML to przede wszystkim:
- skrócenie czasu przestojów oraz czasu wdrożenia,
- sprawna integracja maszyn różnych dostawców w jedną linię produkcyjną,
- zminimalizowanie czasu potrzebnego na szkolenia służb utrzymania ruchu,
- łatwe podłączenie maszyny zgodnej ze standardem PackML do linii/systemu Scada /MES czy sterownika linii
- wymiana informacji pomiędzy maszynami i całymi liniami oraz bazą informacji
- chmurowych
- standaryzacja danych wejściowych i wyjściowych.
Pula możliwości i ułatwień, które można zyskać wprowadzając standard PACKML w zakładzie produkcyjnym sprawia, że stanowi on idealne rozwiązanie dla przedsiębiorstw, którzy nie tylko planują budowę nowego zakładu, ale także chcą unowocześnić i usprawnić pracę już posiadanych maszyn.
Jeśli jesteś zainteresowany takimi rozwiązaniami lub audytem procesów produkcyjnych dla Twojego zakładu to prześlij formularz kontaktowy poniżej!