W artykule przeczytasz:
- przykłady wykorzystania cyfrowego bliźniaka w przemyśle
- możliwości, jakie daje zastosowanie tej technologii w produkcji
- wyzwania, z jakimi wiąże się implementacja
Jaką perspektywę daje Cyfrowy Bliźniak?
Wyobraźmy sobie, że posiadamy wirtualne odzwierciedlenie naszych procesów produkcyjnych w czasie rzeczywistym, dzięki któremu jesteśmy w stanie testować efektywność i wykrywać ryzyko zmian w produkcji, zanim wprowadzimy modyfikacje w rzeczywistym środowisku. Taką modyfikacją może być, na przykład zatrudnienie pracowników, optymalizacja ustawienia maszyn na hali lub przepływu produktu czy półproduktów przez ciąg technologiczny. Dla integratorów robotów przemysłowych, zalążkiem cyfrowego bliźniaka są wirtualne symulacje stanowisk zrobotyzowanych. Skracają one programowanie i konfiguracje zachowania robota w rzeczywistym środowisku.
Cyfrowy bliźniak może zapobiec stracie czasu i pieniędzy na przeprojektowanie maszyn i podzespołów, testy ich efektywności czy opóźnienia produkcyjne. Mimo, że koncepcja Digital Twin jest jeszcze melodią przyszłości dla większości zakładów produkcyjnych (szczególnie tych mniejszych), to jednak zostaje już wprowadzana przez większych „graczy” na rynku.
Przykłady wykorzystania Digital Twin w Przemyśle
Firma CenterLine miała kłopot z kosztami błędów projektowych swoich maszyn oraz z czasochłonną konfiguracją maszyn w zainstalowanych już systemach. Wykorzystali oni rozwiązanie Delmia firmy Dassault Systèmes. W wirtualnym środowisku wprowadzili modele 3D swoich maszyn i ich fizycznych właściwości oraz operacji produkcyjnych, optymalizując layout rozmieszczenia urządzeń, przepływu materiałów czy poruszania robotów przemysłowych. Jak twierdzi firma CenterLine, cyfrowy bliźniak pomógł zredukować problemy związane z poprawkami ich systemów nawet o 90%, a czas programowania fizycznych urządzeń o 75%. To nad wyraz imponujące wyniki.
Drugim przykładem jest współpraca firmy Siemens oraz Volkswagen. W fabryce niemieckiej firmy stacjonuje stanowisko zrobotyzowane, które współpracuje ze stołem obrotowym, na którym umieszczane są drzwi od bagażnika samochodu. Stanowisko oprócz zabezpieczeń w postaci wygrodzenia, posiada także drzwi bezpieczeństwa, przez które wprowadzana jest tylna klapa samochodu. Podczas jej umieszczania na stole obrotowym stanowisko zatrzymuje się, aby nie doprowadzić do niebezpiecznych sytuacji z udziałem pracowników. Drzwi bezpieczeństwa, robot przemysłowy oraz stół obrotowy, a także przebieg całego procesu posiadają swojego bliźniaka cyfrowego i zostały przetestowane w wirtualnym środowisku, aby zapobiec wypadkom przy pracy i stratom materiału.
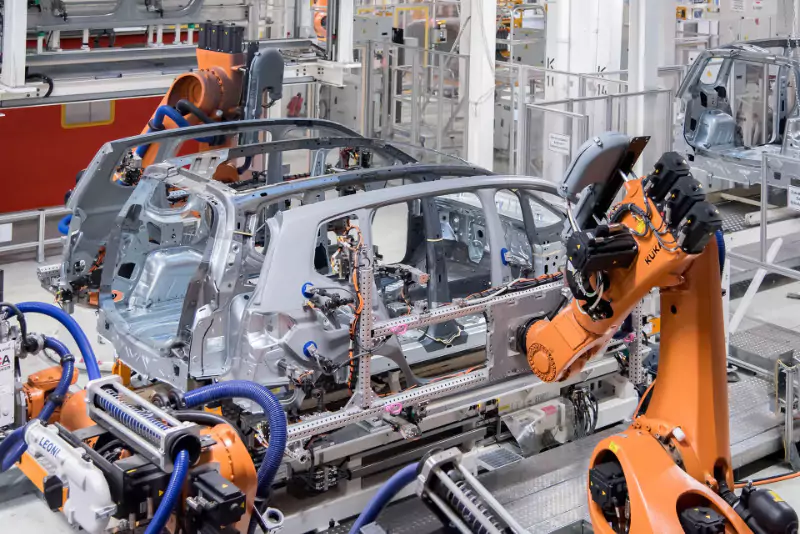
źródło zdjęcia: strona siemens.com
W fabrykach Volkswagena standardem jest wirtualne uruchomienie linii produkcyjnych lub nowych urządzeń na istniejącej linii. Celem jest jak najkrótsze zatrzymanie produkcji w momencie testów i uruchamiania nowych maszyn.
General Electric specjalizuje się w optymalizacji kosztów, dzięki wykorzystaniu Cyfrowych Bliźniaków. W jednym z projektów wypracowali dla klienta wydajniejsze rozwiązanie do konserwacji zasobów. Jednym z zadań inżyniera procesu klienta było wprowadzanie danych do oprogramowania, jednak zbyt długi był czas przeznaczany na tę czynność. Wprowadzenie nowego oprogramowania przyniosło oszczędności wyceniane przez klienta na 85000$ rocznie.
Równie ciekawy przykład, lecz z zupełnie innej bajki istnieje w Formule 1. Ten sport również korzysta z konceptu Digital Twin. Bolid posiada, tak zwane skrzydła przednie i tylne, które służą generowaniu docisku bolidu do podłoża, a tym samym utrzymania pojazdu w zakrętach przy wysokich prędkościach. Testy wpływu siły oporu powietrza na bolid (aerodynamika) wykonuje się często w środowisku wirtualnym, co daje duże oszczędności dla zespołów Formuły 1.
Możliwości i korzyści wykorzystania Cyfrowego Bliźniaka w produkcji
Digital Twins opierają się na zbieraniu danych z rzeczywistych obiektów, a następnie przetwarzaniu tych danych w cyfrowym modelu. Daje to możliwość dokładnego odwzorowania zachowania maszyn i urządzeń w różnych warunkach.
Optymalizacja procesów produkcyjnych
Symulacje różnych scenariuszy ciągu produkcyjnego i analiza wyników pomaga zidentyfikować najefektywniejsze metody produkcji, nie ryzykując ich zakłócenia. Skracamy dzięki temu wypracowanie optymalnego działania procesów. Ponadto symulacje przynoszą korzyść w postaci eliminacji nadmiernego zużycia materiałów oraz energii.
Zarządzanie utrzymaniem ruchu
Digital Twin posiada duży potencjał w przewidywaniu awarii. Monitorowanie maszyn w czasie rzeczywistym i predykcja ich stanu oszczędza koszty na planowanych konserwacjach oraz przestojach w produkcji.
Projektowanie i testowanie produktów
Cyfrowe Bliźniaki umożliwiają przeprowadzenie szczegółowych testów nowych produktów w wirtualnym świecie, co wpływa na redukcję kosztów prototypowania oraz skrócenie czasu wprowadzenia ich na rynek.
Z jakimi wyzwaniami wiąże się wdrożenie tej technologii?
Digital Twin jest technologią automatyzacji produkcji, która niesie ze sobą niewątpliwe korzyści. Istnieje jednak wiele wyzwań, z którymi należy się zmierzyć chcąc wdrożyć cyfrowego bliźniaka. Niektóre z tych wyzwań mogą być szczególnie trudne do pokonania dla mniejszych firm, które dysponują ograniczonymi zasobami budżetowymi. Podstawowymi wyzwaniami są przede wszystkim:
Modelowanie i symulacja
Tworzenie kompletnych i dokładnych modeli 3D urządzeń, linii produkcyjnych i całych zakładów to złożony proces wymagający zaawansowanej inżynierii i wiele godzin czasu pracy.
Skomplikowana integracja danych
Gromadzenie, scalanie i synchronizacja dużej ilości danych z różnych źródeł (czujniki, systemy ERP, CAD, itp.) stanowi duże wyzwanie, szczególnie w dojrzałych, zdecentralizowanych organizacjach.
Bezpieczeństwo danych
Dane przechowywane w cyfrowych fabrykach muszą być chronione przed cyberatakami, co wymaga wdrożenia solidnych rozwiązań bezpieczeństwa.
Potrzebne kompetencje pracowników
Wykorzystanie pełnego potencjału Cyfrowych Bliźniaków wymaga przeszkolenia pracowników w zakresie nowych narzędzi i technologii.
Koszty
Wdrożenie technologii wymaga inwestycji w infrastrukturę, np. czujniki, systemy zbierania i analizowania danych, oprogramowanie do modelowania i symulacji. Ponadto należy pamiętać o kosztach konserwacji sprzętu, przetwarzania dużych ilości danych czy aktualizacji oprogramowania.
Po zapoznaniu się z powyższymi wyzwaniami, możemy już sobie wyobrazić przybliżoną skalę kosztów, jakie poniosą przedsiębiorstwa inwestujące w Cyfrowego Bliźniaka. Jednak nie musimy, a wręcz nie powinniśmy zaczynać takiej implementacji od całego procesu technologicznego. Symulacje pojedynczych procesów będą nieporównywalnie tańsze, a przy tym nauczymy się postępować z Cyfrowymi Bliźniakami. Mimo, że jest to jeszcze przyszłość i abstrakcja dla wielu polskich zakładów, to zdecydowanie warto śledzić postęp tej technologii.
Przyszłość Cyfrowych Bliźniaków
Przyszłość technologii Cyfrowych Bliźniaków jawi się jako niezwykle obiecująca. Można wyróżnić kilka kluczowych trendów, które będą kształtować rozwój tej technologii w nadchodzących latach.
Rozwój IoT
Coraz większa liczba czujników i urządzeń IoT będzie dostarczać ogromne ilości danych (Big Data), a zaawansowane algorytmy analizy pozwolą na jeszcze dokładniejsze modelowanie i symulację.
Integracja z łańcuchem dostaw i cyklem życia produktu
Cyfrowe Bliźniaki zostaną zintegrowane z całym łańcuchem dostaw, umożliwiając optymalizację procesu od projektowania do utylizacji. Dane z Cyfrowych Bliźniaków będą wykorzystywane do ulepszania produktów w kolejnych cyklach życia.
Przetwarzanie brzegowe (Edge Computing)
Przetwarzanie danych bezpośrednio przy ich źródle skróci czas reakcji i zwiększy bezpieczeństwo.
Integracja ze sztuczną inteligencją, AI
Zakłada się, że AI i algorytmy uczenia maszynowego będą w stanie samodzielnie identyfikować wzorce i anomalie w danych, usprawniając diagnostykę i prewencyjną konserwację.
Podsumowując, Cyfrowe Bliźniaki mają potencjał, aby stać się bardzo istotnym elementem transformacji cyfrowej w przemyśle, łącząc świat fizyczny z wirtualnym i otwierając nowe możliwości optymalizacji, innowacji i konkurencyjności. Znacznie łatwiej wejść do tego świata większym firmom, a dla małych i średnich przedsiębiorstw taka szansa jest ograniczona, ze względu na koszty. Jednak z czasem, gdy ta technologia będzie się rozwijać, stanie się przystępniejsza również dla tych mniejszych „graczy”.
W naszych artykułach edukujemy, aby zwiększyć świadomość polskich zakładów o rozwiązaniach i korzyściach płynących z automatyzacji przedsiębiorstwa i przemysłu 4.0. Jeśli chciałbyś to docenić to sprawdź nasze inne artykuły.