Proster articles - sources of professional knowledge
Industry knowledge compiled by specialists for specialists. Benefit from the experience of our experts.
Usefulness of 3D scanning in industrial design

„Usefulness of 3D scanning in industrial design”
3D scanning is a modern, fast and extremely precise technique for acquiring 3D environmental data. Although it is still a kind of technical novelty, the circle of its supporters is gradually growing. What are the advantages of using such measurements and will they work well in industrial design?
What is 3D scanning?
Scanning is the process of reading data (which takes the form of an image/information), capturing it and processing it into electronic form. A 3D scanner is a device that creates a 3D model based on a real existing object. The resulting model is a collection of a huge number of points (file in STL extension), which perfectly represent the scanned object. Currently available 3D scanners (short-, medium- and long-range) create models with precision as low as 0.005mm (5μm) supporting the work of many industries such as medicine (scanning and reconstruction of bones or their fragments, repair of prostheses), construction (inventory of buildings, their internal installations or structures, investigation of potential collisions), surveying (situational and height measurements), shipbuilding (inventories of ships and other marine objects). It is therefore possible to image objects of the widest variety of dimensions and structure, with different scanners being used for scanning, for example, buildings or other objects of complex structure (3D laser scanners), and others for scanning objects that show movement, such as the human body (3D structured light scanners).
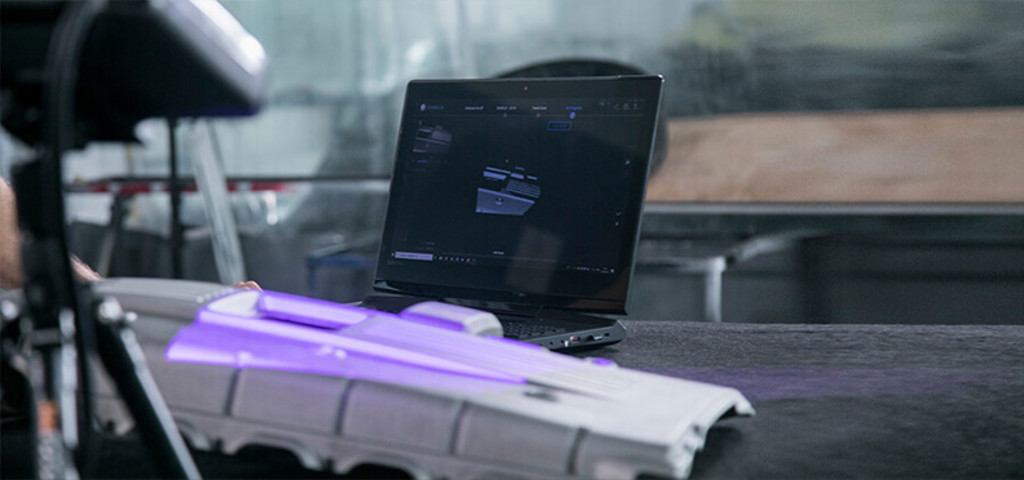
Laser scanners:
Due to the way the distance is measured, there are three types of laser scanners: pulse, phase and triangulation (with a single or dual camera). In the case of pulsed scanner measurement, the emitted light beam is reflected from the surface of the target, and its return is registered in the detector. Based on the measurement of the time between the moment of emission and return of the pulse, the distance of the point from the scanner is calculated. The accuracy of such measurements is estimated at 4 – 10 mm with a scanning speed of up to 50,000 points per second and a maximum range of up to 300 m. In phase scanners, distance is measured by analyzing the phase shift of the wave returning to the detector after reflection from the object compared to the phase of the beam being sent. Phased-array scanners can measure distances with greater precision (4 mm accuracy) and speed (up to about 970,000 points per second), but with a shorter scanning range (up to about 130 m). For industry, triangulation lasers will be the most suitable, as they have the greatest precision in measurement (shorter range, greater accuracy – even to hundredths of a millimeter). The measurement is made by sending a laser beam that falls on the matrix of a digital camera after reflecting off an object.
Różnicując skanery przez pryzmat ich pola widzenia należy wspomnieć także o podziale na skanery panoramiczne, hybrydowe oraz typu kamera – wybór urządzenia każdorazowo zależeć będzie od złożoności i gabarytów mapowanego obiektu. It will also be necessary to take into account other important issues, such as the location of the scanner, the appropriate resolution, the angle of incidence of the laser beam on the object to be scanned, so-called noise, atmospheric conditions, as well as the presence of glass and shiny surfaces that may reflect the beam in the wrong direction.
Scanning for the industry:
Analyzing the topic of modern measurements through the prism of PROSTER’s experience, it is worth talking about two main areas in which 3D scanning will be an invaluable support. The first area, is the need to map the entire production facility, understood as a building facility, in terms of planned future reconstruction/expansion, etc. An inventory carried out by scanning will give an image that is accurate to the smallest details (especially those invisible to the eye). This solution will be particularly helpful for facilities built decades earlier, for which it is difficult to find reliable design documentation or any technical documentation. Thanks to the measurements taken, the designer will be able to make an analysis of the condition of the structure, study the verticality of the elements and the shape and structure of existing deformations. The high resolution of the resulting point cloud will make it possible to accurately detect existing cavities and assess their size. Such a collection of information will allow to estimate the need for renovation or modernization.
Area two is to perform scans of individual production line components (machine parts) that need to be replaced due to damage or wear. The model of the detail obtained in this way allows for faithful reproduction. An example of this type of implementation at PROSTER was the design of a glow chamber, which was to be a copy of an existing solution (made in casting technique), working as a component of a larger production line. Precision craftsmanship was therefore crucial for a perfect match between old and new components. Against this background, it is important to emphasise the high usefulness of scanning equipment especially in working with complex objects, where traditional methods of measurement would not only be time-consuming, but also subject to a significant risk of error, and very often simply impossible. The use of laser scanning as a measurement method in industrial design makes it possible to record the actual and accurate condition of an object and provides the precise data needed to create technical documentation. Importantly for designers, it is possible to export the point cloud to the CAD environment for models, sections, projections and subsequent studies.
Author: Marzena Fijałkowska
Bibliography:
- Magdalena Bernat, Alicja Byzdra, Mariusz Chmielecki, Przemysław Laskowski, Janusz Orzechowski, Slawomir Rzepa, Jakub Szulwic, Patryk Ziółkowski, Application of terrestrial laser scanning and
data processing: inventory and inspection of building structures. Technology Review and Application Examples, GEOMATICS Series, Gdansk University of Technology Publishing House, Faculty of Civil and Environmental Engineering, 2016, pp. 11