Proster articles - sources of professional knowledge
Industry knowledge compiled by specialists for specialists. Benefit from the experience of our experts.
Solutions used in the food industry for electrical systems
What is crucial here is the product, as well as the way it is processed through the use of modern production lines, equipped with electrical systems that provide a constant power supply.
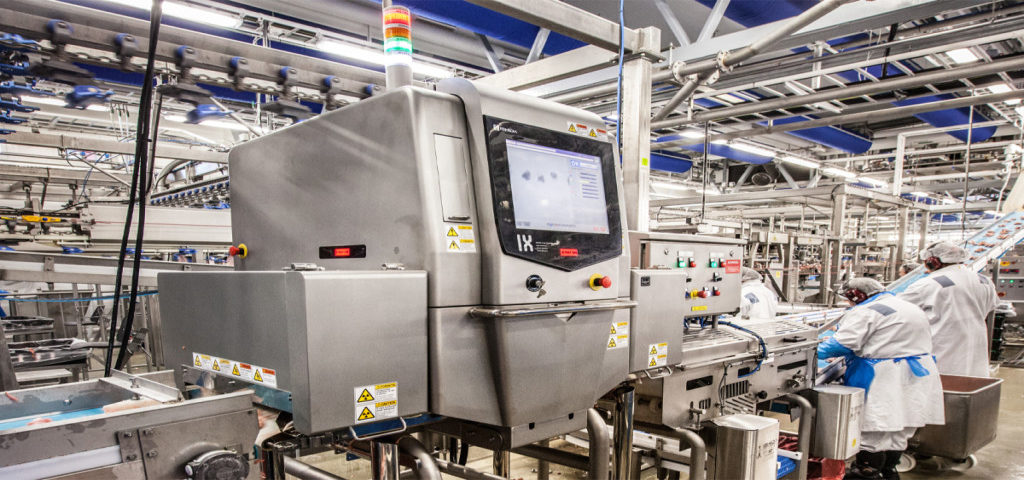
Hygiene standards (HACCP Directive)
The starting point for discussing electrical solutions used in the food industry is safety considerations understood here primarily in terms of keeping production lines clean. This is because the slightest contamination of a product can result not only in production losses, but above all carry a health risk for consumers. In order to ensure the highest level of production safety, all elements of the production line, including supply installations, must be carried out to so-called hygienic standards, which are defined by the Hazard Analysis and Critical Control Points System (HACCP). It is a set of interrelated procedures, implementing as a whole a food safety management system.
In this system, the main focus, related to food surveillance, is on the causes of hazards directly at the site. In this way, health risks associated with raw materials, additives and auxiliary materials, personnel, machinery and equipment, as well as the technological process are prevented or eliminated before the product is manufactured.
Switchgear enclosure
PROSTER’s team of experienced specialists, which has been providing electrical engineering solutions for the food industry for years, has repeatedly faced the challenges of designing and carrying out electrical installations. The biggest of these seems to be the extreme working conditions in such plants, occurring in particular during the process of disinfection of machines, process lines, as well as entire production units. Taking into account the requirements of the HACCP system, already at the design stage, PROSTER specialists place a strong emphasis on the use of elements and components that minimise or exclude the risk of harmful effects of moisture, resistance to chemicals, dirt deposition, etc.
One such example is the use of stainless steel switchgear enclosures. Indeed, corrosion is a serious problem that affects not only the switchgear itself (lowering its mechanical strength and the durability of the installation), but also its immediate environment, including the food product on the production line. Equally important is the use of locks in a hygienic design that allows to minimise or completely eliminate the possibility of dirt deposition. A common solution is to use switchgear enclosures with a sloping roof. This solution further reduces the areas where dirt can accumulate.
Another thing worth mentioning is the method of cable entry into the switchboard, which is carried out from underneath the cabinet through cable glands made to hygienic standards. Silicone gaskets used both at the doors and at the unscrewable parts of the enclosure are also a very important element of the switchboards.
Cable routes
Also in the case of cable routes, resistance to corrosion and dirt is of colossal importance. Hence, mesh troughs are the preferred solution. They are used in electrical installations that undergo hygienic cleaning. Key features include a design that does not retain dirt and moisture. In addition, in mesh trays, cables have better cooling.
Corridors of this type are a very flexible solution in terms of the possibility of adapting the cable route system to specific object conditions. The basic components of the system are galvanised or made of stainless steel.
To ensure very high quality hygienic standards, the assembly of cable routes is done by welding – it minimises the presence of moving parts (connectors, screws) that can fall into the product on the line. It is worth noting that cables in hygienic installations are laid and packaged individually, they are not grouped into cable bundles.
The entire article can be read here: https://foodindustry-support.pl/rozwiazania-stosowane-w-przemysle-spozywczym-instalacje-elektryczne/