Proster articles - sources of professional knowledge
Industry knowledge compiled by specialists for specialists. Benefit from the experience of our experts.
Key features of robotic palletising and depalletising
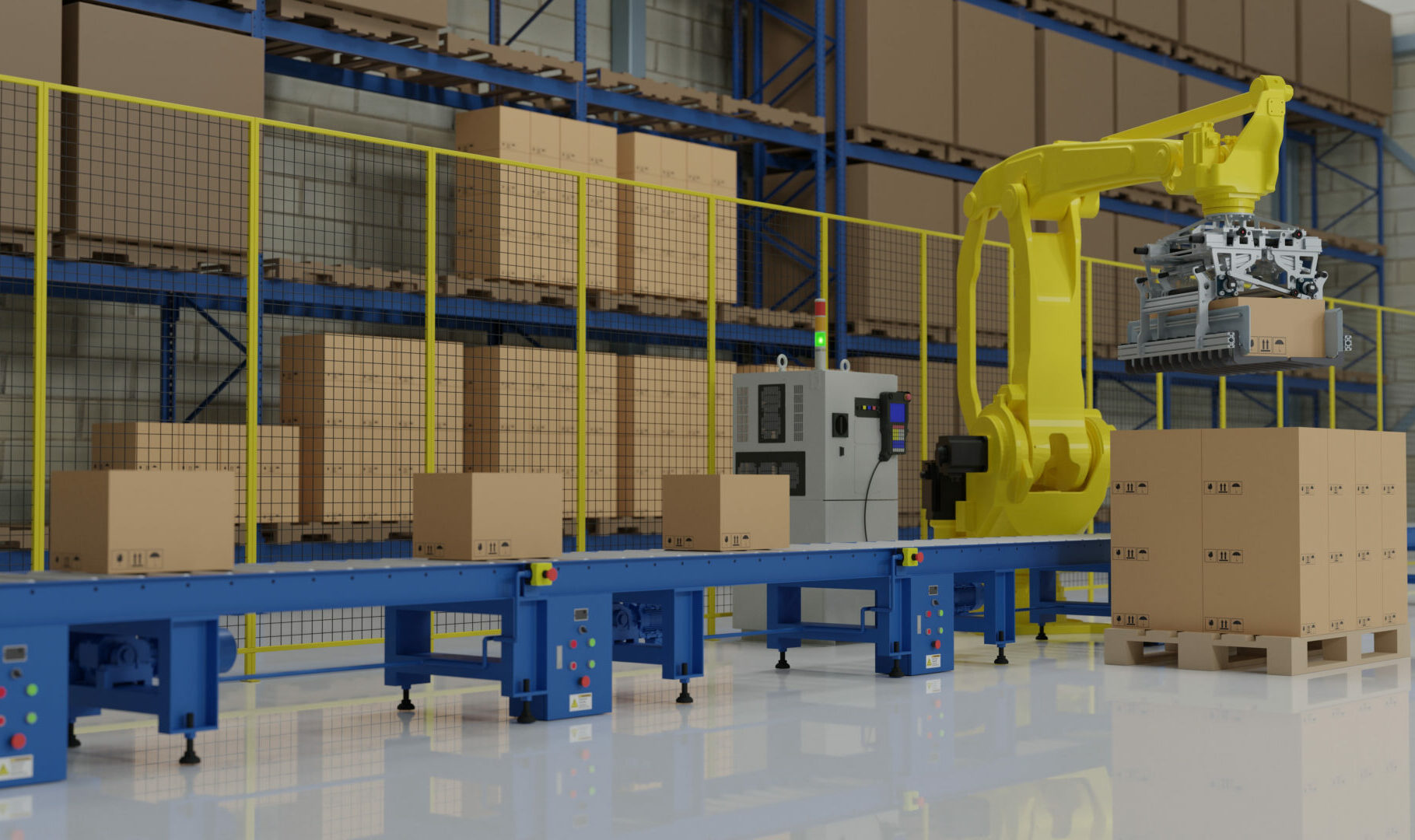
This article is for you if:
- You want to find out in which cases the robotisation of these processes is cost-effective
- You want to find out what influences the costs of robotic palletisation
- You want to find out how to finance such an investment.
Palletising and depalletising are processes that play a significant role in many manufacturing and distribution companies, especially the ones that process goods on a mass scale.
In palletising, products or goods are placed on pallets in specific patterns, according to a certain specifications and customer’s requirements. In depalletising, on the contrary, goods are taken off the pallets in a controlled and safe manner, enabling faster processing of products in the warehouse and on the production line. Both processes serve to streamline logistics, reduce costs and minimise damage to goods during transport or further processing.
Robotisation of these processes can not only save time and money, but also the safety of workers who can take on less monotonous and physically demanding work.
Robotic palletising and depalletising – benefits
Robotic palletising is an increasingly popular method of automatically stacking products on pallets. Demand for robotic depalletising is also growing among manufacturing companies. This is not surprising, while the benefits of automating these processes far outweigh the costs spent on its implementation:
- Increased line efficiency – industrial robot palletising increases process efficiency, resulting in more efficient distribution of product in less time and a rapid return on investment
- Reducing the staffing problem – as more and more manufacturing companies are struggling to find people to work with. According to ManpowerGroup’s ‘Talent Shortage’ report, as many as 45% of manufacturing companies are struggling to fill positions with production workers
- Flexibility, ease of configuration – the robot can be programmed to handle different types of products and pallets and quickly adapted to a new type of component, giving great flexibility in the process
- Improved working conditions – replacing monotonous tasks in favour of operating an industrial robot
- Safety of workers – they do not have to deal with manual stacking of heavy and bulky products
- Continuity of work, elimination of downtime – the robot is able to work even 24/7, enabling uninterrupted processes of unloading and preparing products for transport
- Precision and repeatability – the programmed robot enables accurate positioning of products on pallet stacks
- Monitoring and reporting – robotic workstations can be equipped with systems that monitor the entire process and report on results, allowing for continuous process improvement and efficiency
- Integration with technologies – the robot can be integrated with, for example, a barcode scanning system, vision system or weight control, further increasing process efficiency
All these benefits make the robotisation of palletising and depalletising processes increasingly applicable to the production and storage of products, allowing companies to increase their competitiveness and distribution capacity.
Impact of product packaging on palletising
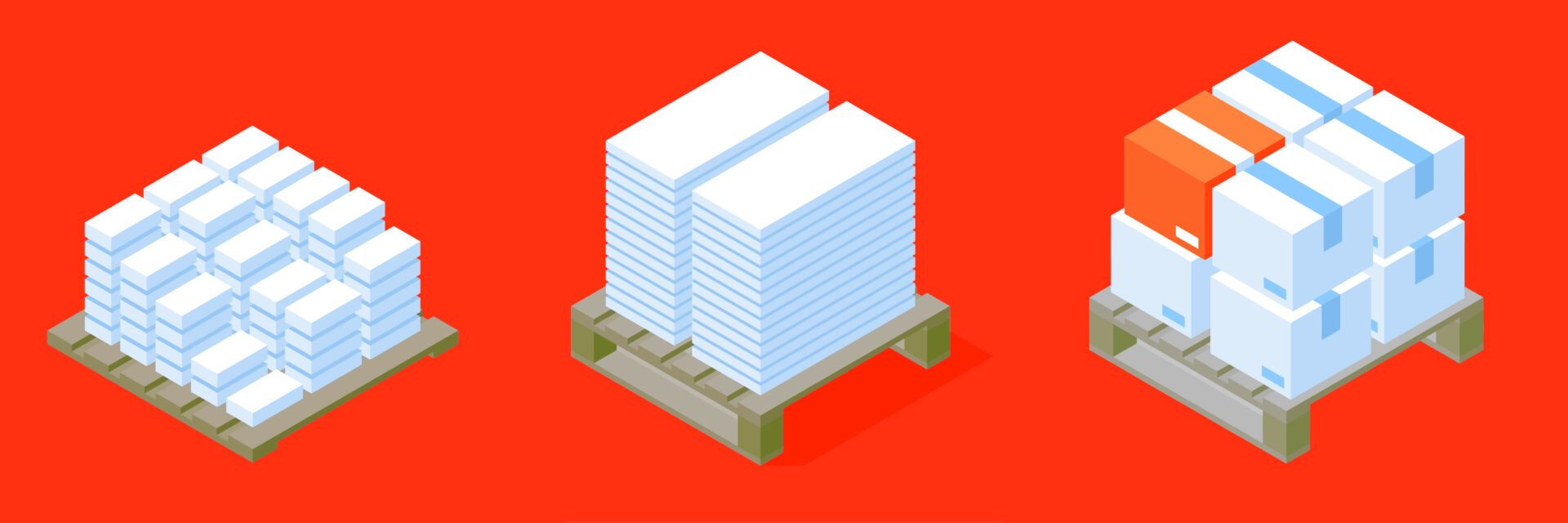
The most important factor defining these processes is the type of product and packaging. Packs, bags, buckets and, most commonly, cartons – for each, the design of a suitable robot gripper is required that is able to transport the material from the production line to the pallet. While for bags of building material we do not need precision to one millimetre, for open cartons very high accuracy is required. To better illustrate why this is the case, let us use this example.
Open-top cartons (in which fruit and vegetables are often transported from producers and distributors to retailers) are not the same type of packaging as closed cartons. They differ primarily in terms of stiffness, which is much lower for open cartons. The precision of the palletising and depalletising of fruit and vegetables has to be very advanced in their case, due to the fact that they have teeth that position each layer on the pallet. There is also the aspect of the humidity of the packaging, which further reduces its rigidity.
Details like these influence the fact that different types of packaging require a gripper that is adapted to the products in order to ensure the safety and reliability of the process. This generates costs and its size can depend on many aspects.
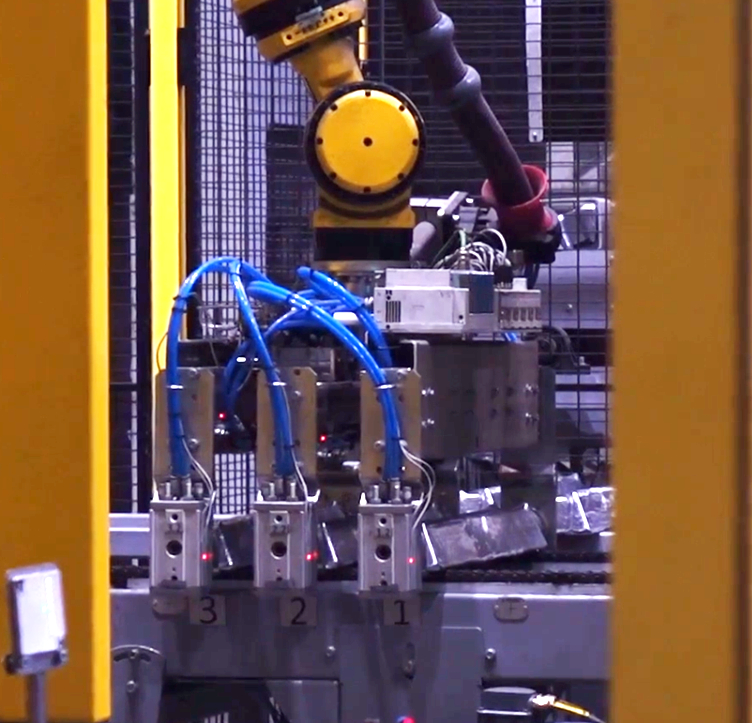
Gripper for palletising aluminum bars
Costs of implementing a robotic system
The decision to implement automation and robotics should be a deliberate process in order to reduce as much as possible the expenses associated with its implementation, or possible redesign with increasing customer needs.
The price of automating palletising and depalletising processes primarily depends on the process capacity needed, but also on the shape and weight of the product packaging. A robot for palletisation can be one of larger costs on a project, and the price is influenced by its type, lifting capacity or maximum reach. Therefore, the price of robotisation in production varies depending on the industries and activities to be automated. The design, testing and installation of the system itself can also be a significant cost, requiring specialist knowledge and experience. However, the money spent on these activities can be reduced when choosing an existing solution on the market. Further funds should be budgeted for associated equipment and systems (conveyors, turntables, automation components, mechanics, electrics, control systems, production management 4.0, etc.), the price of which will depend on their quality.
It is worth noting here that cost reduction is achieved by choosing a partner who takes care of all the work comprehensively – from needs analysis and consultancy, through the design and implementation of mechanics, automation and electrics, to the training of the client’s operators and service care under warranty. We then do not waste money on additional costs spread over subcontractors, but receive care from one company comprehensively.
Depending on the scale and complexity of the project, the cost of implementing a robotised palletising process can start at a few tens of thousands of zlotys for simpler systems, and range from a few hundred thousand to over a million zlotys. There is really no upper limit, as it depends on the customer’s production needs, required efficiency and consequently the number and scope of automatic palletising stations. Fortunately, there are various options for financing such a way of improving production.
Ways of financing robotisation
The robotisation of production usually requires significant financial investment. In addition to financing it from own resources, there are several ways to raise funds for investment:
- Bank credit – banks offer various types of investment loans
- Leasing – a form of financing in which a robotic system is leased in exchange for regular lease payments
- Robotisation allowance – there is a robotisation allowance in Poland, which consists of the possibility of an additional deduction from the tax base of 50% of the tax-deductible costs incurred for robotisation (including the purchase of robots, machinery and equipment; intangible assets necessary for the correct launch of the robots; leasing fees on fixed assets; or costs of operator training)
Is it cost-effective to robotise the palletisation or depalletisation process?
Investing in the robotisation of these processes can pay off, but the final assessment of profitability depends on a number of factors.
- Scale of operation – if a company has a high demand for palletisation, automating the process can result in significant savings in time and manpower. Automated robots can run for longer hours without the need for interruptions, which can speed up the process and increase productivity, and workers previously involved in production processes can be reallocated to other, less physically engaging work
- Labour costs – if costs such as wages and insurance are significant, the use of robots can save money. Robots do not require wages, do not get sick and do not need rest
- Errors and quality – robots are programmable and operate with high precision, minimising the risk of human error. This results in greater consistency and accuracy in palletisation, which in turn can reduce waste and complaints
- Cost and return on investment – the costs allocated to robotising the process (mentioned in the section above) should be considered. It is also important to assess the time to return on investment (ROI) and estimate the potential savings or productivity gains that result from automating the palletisation process.
In our articles, we educate so that the decision to robotise and automate production is an informed and thoughtful one. If you would like to appreciate this, please read our other articles.