Assembly of bottling line in the brewing industry for KHS
Partner
KHS Group is one of the world leaders in the production of bottling and packaging machines. With over 150 years of history, it is one of the most experienced suppliers of this type of machines on the market.
Project: Assembly of bottling line machines for the brewing industry
Place of project implementation: Belgium
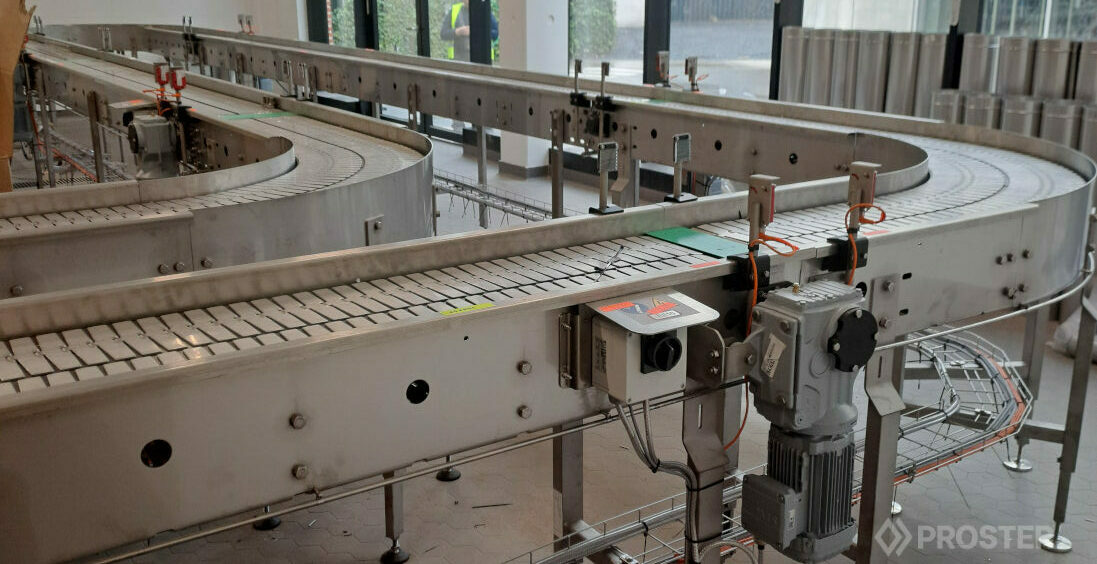
Mechanical assembly of machines
The scope of mechanical work at the plant included the assembly of machines for:
- filling KEG barrels,
- cleaning, fit control, rotation, closing of barrels,
- quality control vision system, HMI panels,
- KEG barrel conveyors and pallet conveyors,
- cells with robots for palletizing and depalletizing,
- palletizer, pallet wrapper, pallet storage machine
- assembly of machines for remote diagnostics services.
The assembly began with unloading the machines to their destination according to the line layout. It also involved the positioning, alignment and assembly of machines, lubrication and cleaning systems for chains, platforms and stairs. Then configuration of mechanical functions of machines, safety installations and documentation of changes.
Electrical installations
The scope of electrical work at the plant included powering machines and devices included in the technological line. These machines were mentioned earlier in mechanical scope. The basic tasks included laying main cable routes and power and control cables, connecting machines, assembling and connecting the main switchboard and control cabinets of individual machines, safety curtains, emergency stop buttons, HMI operating panels and junction boxes. Additionally, I/O control, installation and documentation inspection and change documentation were an integral part of this work.
Benefits for our Partner
We are a regular partner of KHS in electrical and mechanical installations, hence the work is performed with repeatable, highest quality
-
Full knowledge of technical issues in the industry
ensured self-sufficiency and allowed the project to be completed on time, without any unforeseen additional costs
-
Flexibility towards the client
by increasing resources on the project at key stages
-
High quality of work performed, known to the customer
ensures long-term safety of the production line and minimizes the risk of failure
-
Implementation with a reliable partner
We perform work confirmed by the ISO 9001 quality management system certificate (check in the footer)
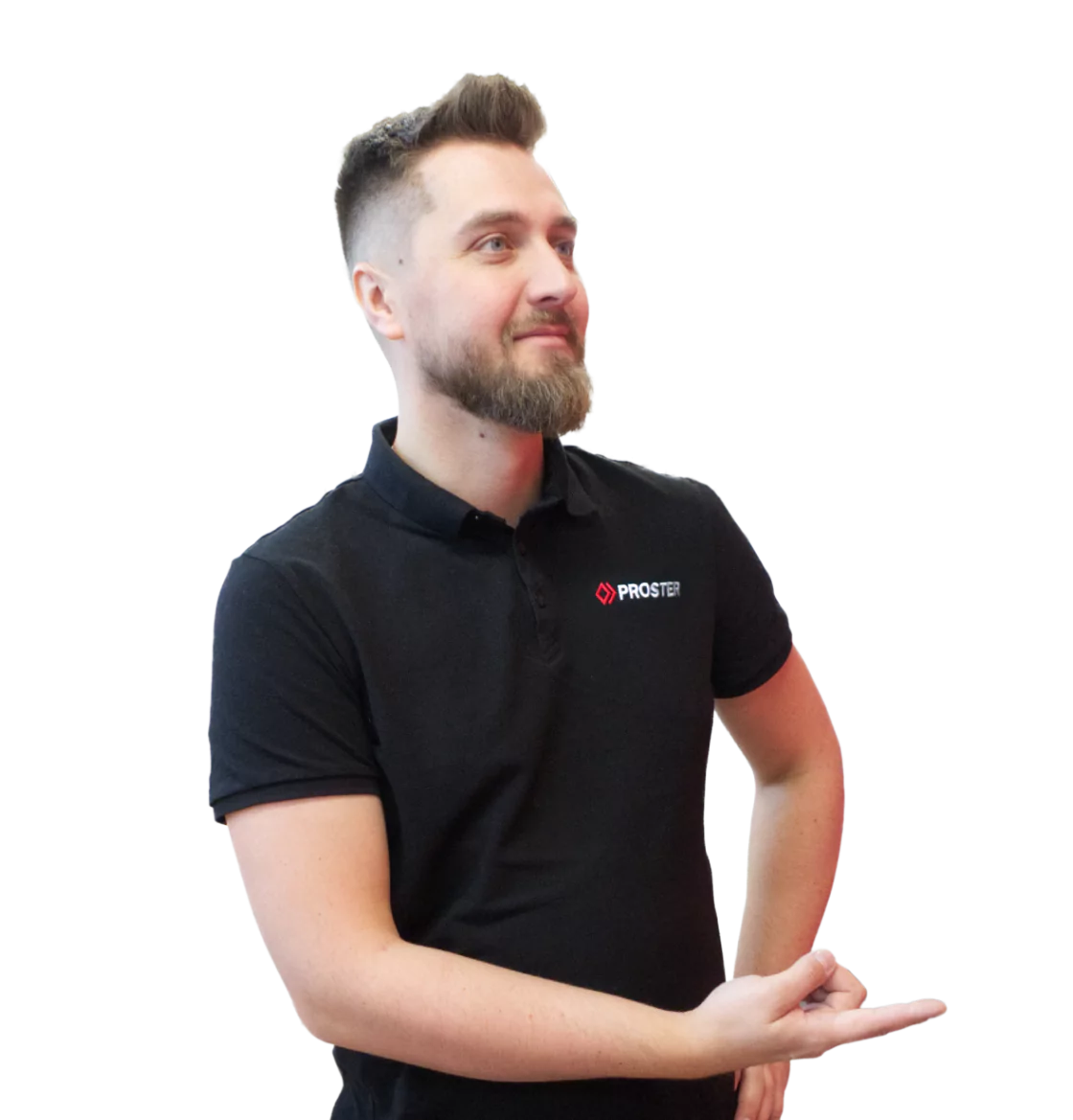