Artykuły Proster - źródła profesjonalnej wiedzy
Branżowa wiedza zebrana przez specjalistów dla specjalistów. Skorzystaj z doświadczenia naszych ekspertów.
Integrator Robotów Przemysłowych - ważne w wyborze firmy
Jak sprawić, aby wdrożenie robotyzacji zakończyło się sukcesem i naprawdę zwiększyło wydajność produkcji, przynosząc tym samym zyski dla firmy? W jaki sposób osiągnąć szybki zwrot z inwestycji?
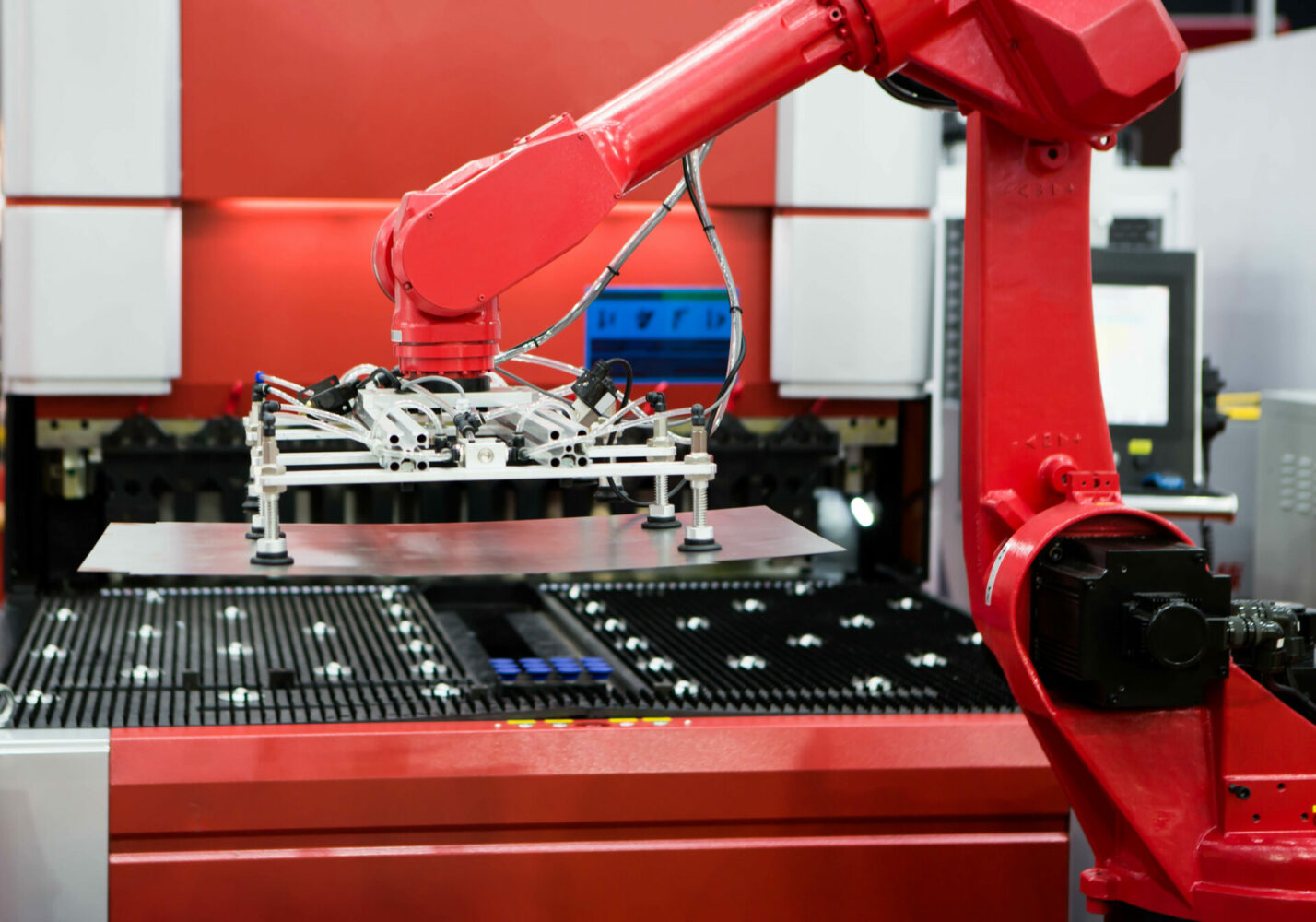
Może wolisz posłuchać? 🔊
Coraz więcej firm decyduje się na wdrożenia systemów zrobotyzowanych w procesach produkcyjnych swoich zakładów. Korzyści jest wiele – od podniesienia poziomu bezpieczeństwa, przez wzrostu wydajności i powtarzalności, aż po mniejsze uzależnienie od personelu. Jednak brak świadomości istotnych etapów projektu wdrożenia może doprowadzić do błędnego wyboru integratora, a w konsekwencji do nierentownej inwestycji.
Ten artykuł jest dla Ciebie, jeśli:
- Chcesz dowiedzieć się jak wdrożyć robotyzację, która realnie usprawni Twoją produkcję,
- Chcesz zwiększyć wydajność produkcji w swoim zakładzie,
- Chcesz przygotować się do wdrożenia robotów przemysłowych,
- Szukasz konkretnych wskazówek, dzięki którym wdrożenie osiągnie sukces.
Na co zwrócić uwagę przy wyborze integratora robotów?
Przejdźmy przez kolejne etapy wdrożenia automatyzacji i zobaczmy co na każdym z nich jest ważne zarówno z perspektywy klienta, jak i integratora takich rozwiązań – co pomoże lepiej zrozumieć cały proces i wyłapać ryzyka, którym możemy zapobiec jeszcze na etapie wyboru firmy wdrażającej.
Etap 1 – Wizja lokalna produkcji
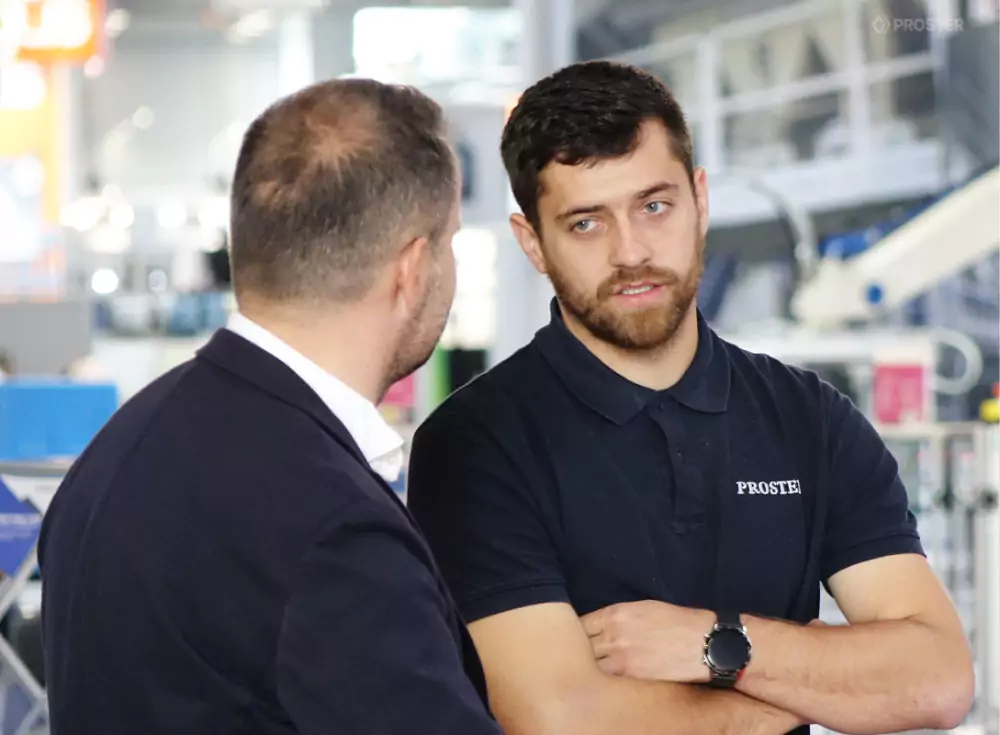
Wizja lokalna, wykonywana przez integratora robotów przemysłowych, polega przede wszystkim na odpowiednim rozeznaniu potrzeb zakładu produkcyjnego. Na tym etapie muszą paść pytania od integratora o najważniejsze powody zainteresowania robotyzacją, potrzeby oraz problemy zakładu, ponieważ bez tego nie zostanie ustalona wspólna wizja. Ponadto przynosi to niezwykle ważne korzyści:
- Integratorowi pozwoli to skupić się na rozwiązaniu problemów zakładu, natomiast sam zakład będzie upewniony o dobrej drodze,
- Integrator będzie mógł spojrzeć szerzej, na procesy całego zakładu. Będzie w stanie znacznie trafniej doradzić w wyborze rozwiązania
Integrator może na podstawie swojego doświadczenia, w przybliżeniu zarysować co sprawdza się w branży, jednak dla każdego konkretnego przypadku będzie to wyglądało inaczej. Do tego jest potrzebna głębsza analiza.
Etap 2 – Analiza procesów wytwórczych oraz potrzeb klienta
We wstępnej analizie potrzeb przed wdrożeniem określa się liczbę produkowanych detali, aby założyć obciążenie pracy stanowiska zrobotyzowanego. Musi być bowiem założona konkretna wydajność procesu przed przystąpieniem do projektu – to jeden z najistotniejszych parametrów, który ustala cel do jakiego zmierza wdrożenie.
Najważniejszym na etapie analizy potrzeb jest poświęcenie odpowiedniej ilość czasu na określenie rzeczywistych wymagań planowanej inwestycji w taki sposób, aby była ona optymalna względem potrzeb i nie zwielokrotniła kosztów poprzez późniejsze przeprojektowania lub niedopasowania. Dodatkowo integrator wspólnie z klientem mogą na tym etapie znaleźć sposób na sfinansowanie inwestycji w formie leasingu, kredytu lub dotacji. Dlatego tak ważny jest wybór integratora rozwiązań zrobotyzowanych, który będzie w stanie dokonać odpowiedniej wizji lokalnej, przeanalizować potrzeby klienta i kompleksowo doradzić jeszcze przed integracją.
Etap 3 – Koncepcja i projektowanie – dobór systemu zrobotyzowanego
Kolejny etap to dobór odpowiedniej technologii oraz przygotowanie koncepcji rozwiązania przez integratora. Należy tutaj zwrócić uwagę, że dobór odpowiedniego systemu pozwala na możliwie tanie zwiększenie wydajności procesu produkcyjnego w miarę wzrastających potrzeb w trakcie użytkowania linii. Oprócz tego odpowiednie rozlokowanie maszyn i urządzeń pozwoli na oszczędność miejsca na hali oraz rozbudowanie linii w przyszłości. W przypadku gotowych rozwiązań robotyzacji, projektowanie zajmuje znacznie mniej czasu pracy konstruktorów mechaniki, robotyków czy automatyków, co bezpośrednio przekłada się na ograniczenie kosztów ponoszonych przez firmę produkcyjną. Integrator powinien na tym etapie przygotować obliczenia zwrotu z inwestycji, aby zapewnić klienta, że zaproponowana koncepcja ma uzasadnienie biznesowe.
Firma wdrażająca robotyzację procesów produkcyjnych powinna bazować na określonych dostawcach automatyki przemysłowej, pozwalających na wyszkolenie pracowników. Posiadanie odpowiednio wyszkolonego personelu, mogącego szybko i skutecznie usuwać awarie oraz wprowadzać modyfikacje we własnych maszynach wpłynie na terminowość realizacji projektu oraz jakość serwisu maszyn i urządzeń. Odpowiedniej klasy wyroby automatyki, ale również mechaniki i materiały elektryczne gwarantują dłuższą żywotność urządzeń i maszyn, które składają się nawet z kilkuset elementów różnych dostawców. Nie trzeba dodawać, że nikt nie lubi awarii, które generują przestoje, a te z kolei przekładają się bezpośrednio na straty.
Etap 4 – Jak symulacje stanowisk zrobotyzowanych przekładają się na mniejsze koszty wdrożenia?
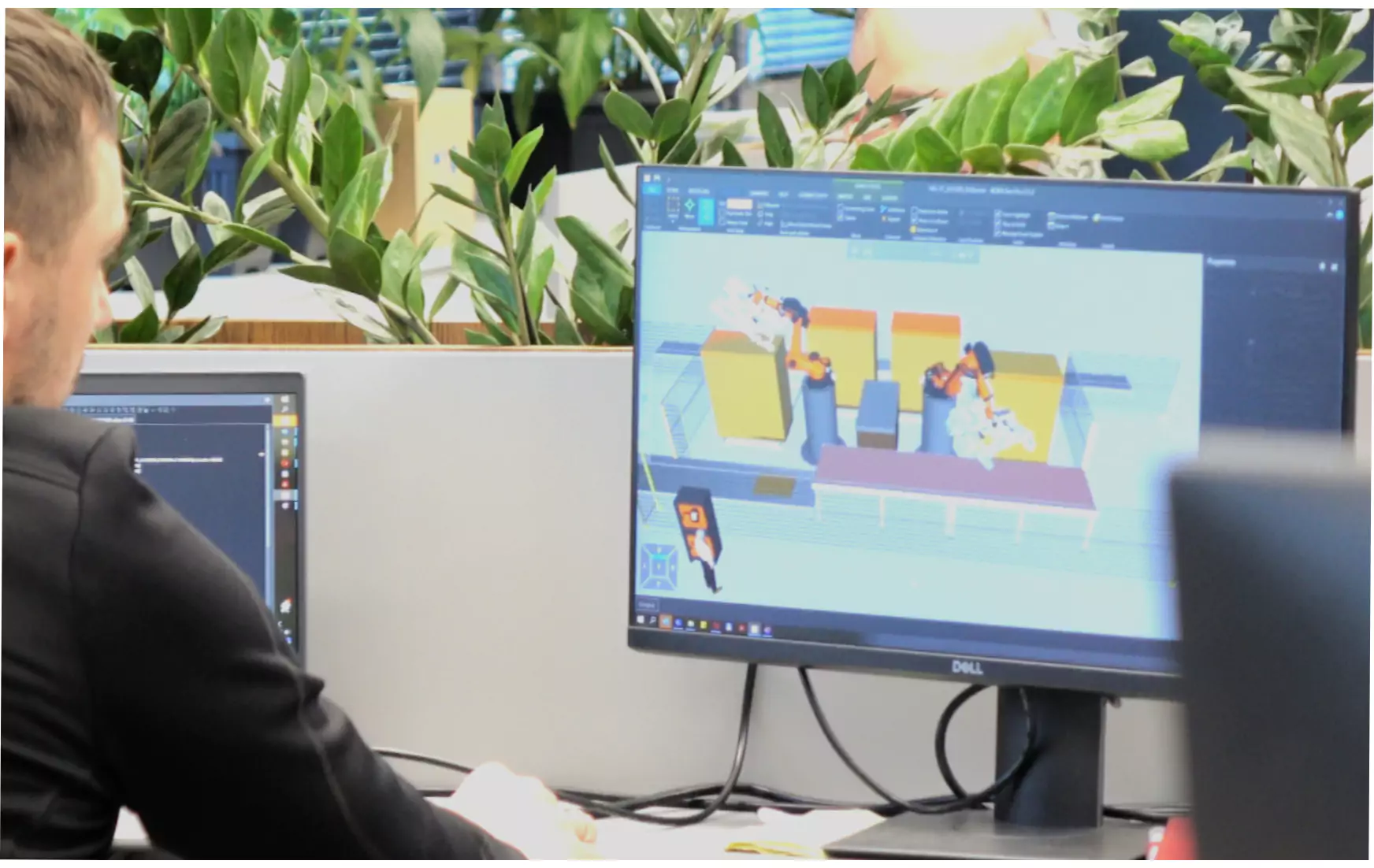
Integratorzy korzystają z programów symulujących stanowiska zrobotyzowane. W przypadku firm zajmujących się projektami kompleksowo, czyli posiadających zespoły automatyków, robotyków, konstruktorów, projektantów elektrycznych, czy elektromonterów, wykorzystywane są również oprogramowania do symulacji mechanicznych i wytrzymałościowych w programach CADowskich oraz projekty elektryczne, np. w programie eplan. Podczas, gdy cały zakres prac odbywa się u jednego dostawcy rozwiązania, pozwala to na zaoszczędzenie czasu na komunikację między różnymi podwykonawcami, a co za tym idzie również zmniejszenie kosztów całego projektu.
Symulacje pomagają przetestować założenia planistyczne (między innymi wydajność planowanej robotyzacji), zweryfikować poprawność zaprojektowanych modeli urządzeń technologicznych, czy optymalnie rozmieścić roboty przemysłowe i współpracujące z nimi urządzenia – nie może bowiem występować kolizji między nimi, a roboty powinny mieć umożliwiony bezpieczny i swobodny dostęp do punktów procesowych. Poza tym symulacje pozwalają przewidzieć zachowania robotów i współpracujących z nimi urządzeń oraz sposób sterowania procesem. Minimalizuje to czas, który zostałby poświęcony na te czynności w rzeczywistych testach stanowiska, co skraca realizację projektu.
Etap 5 – Testowanie – optymalizacja funkcjonalności robotów
Zanim linia wyjedzie na uruchomienie na hali produkcyjnej klienta, jednym z najważniejszych etapów są testy. Najczęściej na hali montażowej integratora odbywa się montaż rozwiązania i testowanie zachowania w warunkach fizycznie odpowiadających procesowi produkcyjnemu. To moment, w którym optymalizuje się funkcjonalności oraz zabezpieczenia procesu przed zagrożeniami, wcześniej niemożliwymi do zasymulowania. Na ten etap, należy przygotować odpowiednie zasoby, zarówno po stronie integratora, ale również klienta. Mowa tu nie tylko o personelu, ale również o materiale produkcyjnym odpowiedniej jakości i ilości, który jest potrzebny do uruchomienia pracy linii z odpowiednią wydajnością. Obu stronom zależy bowiem na jak najszybszym zoptymalizowaniu działania linii w procesie.
Zaraz przed transportem wszystkich maszyn i urządzeń do klienta, o co powinien zadbać integrator, odbywają się testy rozwiązania przy udziale pracowników klienta. Często na tym etapie są formalnie zapisane testy produkcyjne, tzw. FAT (Factory Acceptance Test), które według wcześniej określonych kryteriów potwierdzają spełnienie wymaganych parametrów i wymagań klienta. Po tym etapie klient może kończyć przygotowania do instalacji linii na swoim obiekcie.
Etap 6 – Montaż i uruchomienie linii – przygotowanie hali
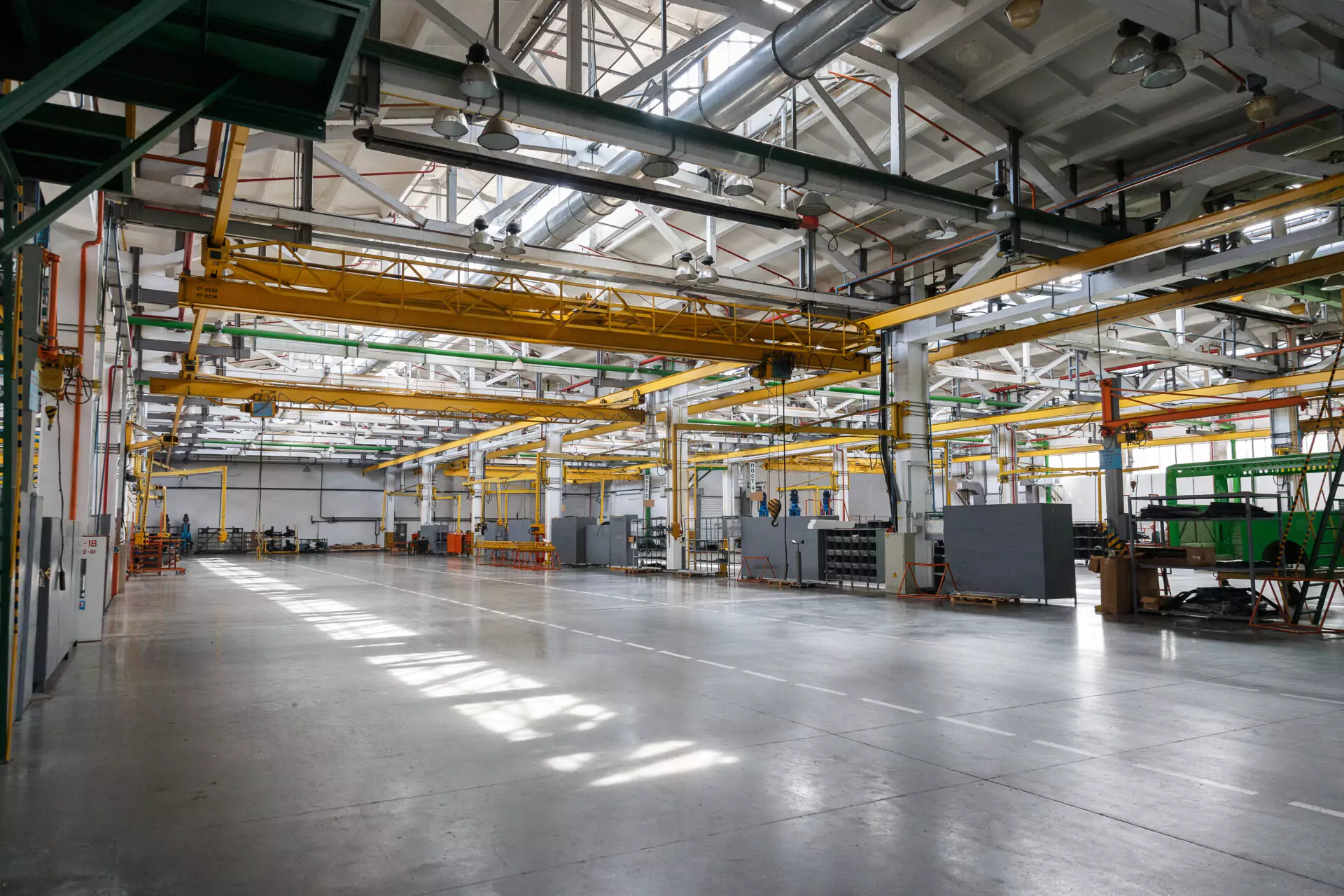
Określenie czasu montażu na hali produkcyjnej jest istotnym czynnikiem dla terminowego uruchomienia linii we właściwym czasie. Należy pamiętać, że prawidłowy montaż jest możliwy jedynie w odpowiednio przygotowanym miejscu docelowym. W teorii wszystko powinno przebiec zgodnie z oczekiwaniami, które zostały zbudowane na testach u integratora. Doświadczenie pokazuje jednak, że nie wszystko da się przewidzieć i na przykład miejsce montażu może nie być zgodne z założeniami klienta – należy bowiem przykładowo przygotować odpowiednio fundamenty pod konstrukcję, czy zapewnić dostęp do źródeł zasilania. Przygotowania hali zależne są od specyfiki projektu. Integrator przy współpracy z klientem powinien przemyśleć ten etap jeszcze przy projektowaniu koncepcji, żeby klient mógł prawidłowo przygotować halę odpowiednio wcześnie i nie wpływać na opóźnienia w terminach realizacji. Skoordynowanie działań na tym etapie jest niezwykle ważne, aby uniknąć nieporozumień.
Etap 7 – Odbiór stanowisk zrobotyzowanych – testy jakości i wydajności
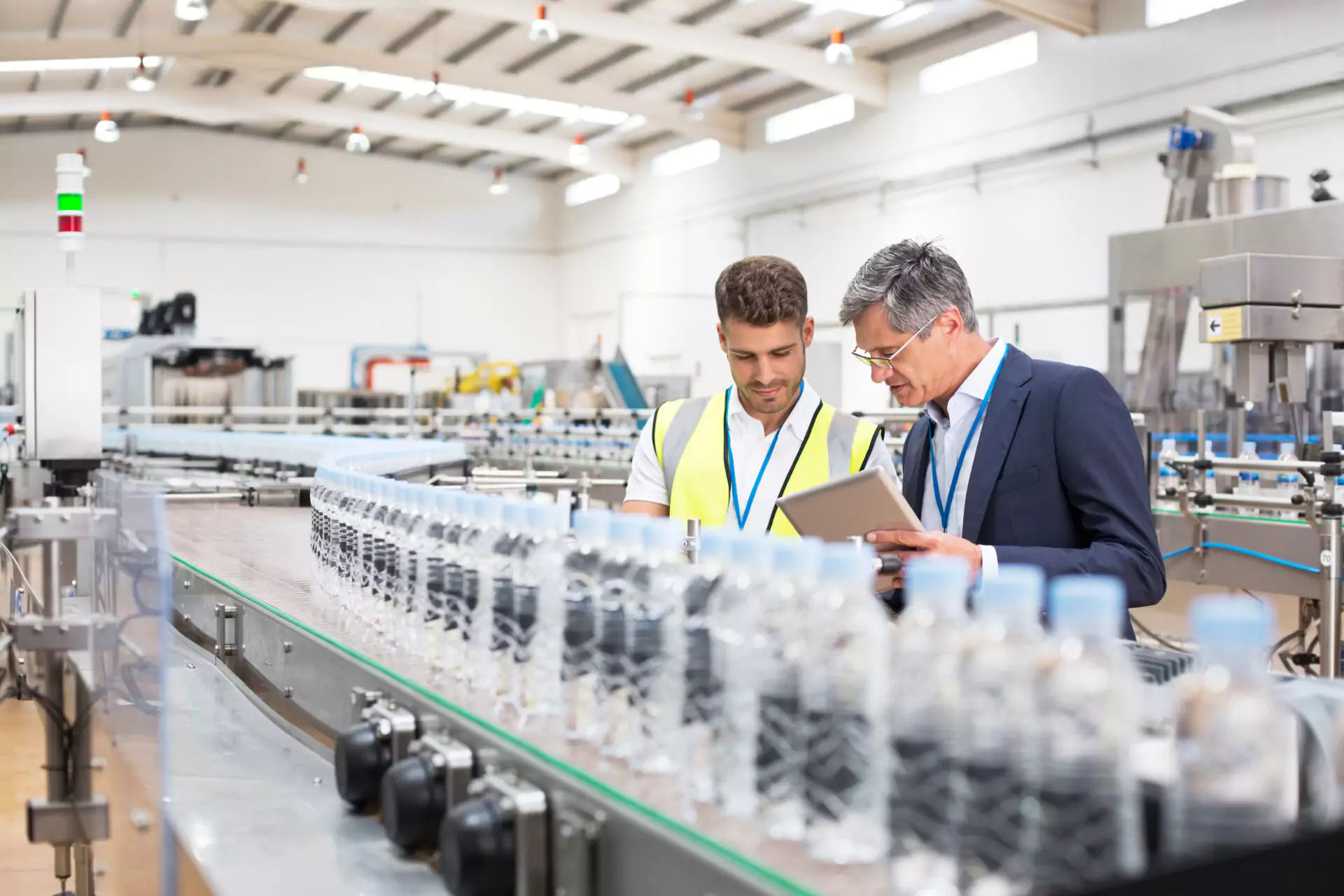
Etap, na który należy przygotować odpowiednie zasoby, zarówno po stronie integratora, ale również klienta. Mowa tu nie tylko o personelu, ale również o materiale produkcyjnym odpowiedniej jakości i ilości, który jest potrzebny do uruchomienia pracy linii z odpowiednią wydajnością. Obu stronom zależy bowiem na jak najszybszym zoptymalizowaniu działania linii w procesie.
Przekazanie linii do odbioru wiąże się również z przeszkoleniem pracowników klienta w zakresie sterowania robotami i urządzeniami współpracującymi, a także serwisowaniem i utrzymaniem ruchu. Zapewni to sprawne usuwanie awarii oraz ograniczenie przestojów na linii. Obowiązkowym uczestnikiem szkoleń musi być także kierownik linii produkcyjnej, który dowie się wszystkiego o nowym procesie, co pomoże mu w lepszym zarządzaniu zespołem. Integrator powinien być zobowiązany od samego początku projektu do przeprowadzenia szkoleń, jak również do przekazania instrukcji obsługi zawierającej informacje o wszelakich szczegółach eksploatacji i dbałości o jakość linii. To podstawa pod ewentualny serwis gwarancyjny.
Kluczowe czynniki dla sukcesu wdrożenia robotyzacji procesów produkcji
Podsumowując, kluczowymi czynnikami dla sukcesu wdrożenia robotyzacji i automatyzacji produkcji są:
- Podejście integratora skierowane na potrzeby i problemy zakładu produkcyjnego
- Założenie rzeczywistych i konkretnych wymagań i celu końcowego
- Dobór odpowiedniego systemu umożliwiającego szybkie i skuteczne zwiększenie wydajności procesu produkcyjnego
- Udział klienta w testach integratora
- Odpowiednio przygotowane miejsce pod montaż rozwiązania na hali produkcyjnej
- Przeszkolenie personelu odpowiadającego za obsługę robotów i całej linii
- Przeszkolenie personelu odpowiedzialnego za serwisowanie i utrzymanie ruchu
- Przeszkolenie personelu z dostarczanych przez rozwiązanie informacji na temat parametrów pracy stanowiska
Nie sposób wydać duże pieniądze, a następnie ciągle serwisować urządzenia i maszyny wchodzące w skład zrobotyzowanego rozwiązania. Dlatego w naszych artykułach edukujemy, aby wybór robotyzacji był świadomy i przemyślany. Jeśli chciałbyś to docenić, to zapoznaj się z innymi naszymi artykułami oraz produktami.