Artykuły Proster - źródła profesjonalnej wiedzy
Branżowa wiedza zebrana przez specjalistów dla specjalistów. Skorzystaj z doświadczenia naszych ekspertów.
Monitorowanie produkcji w czasie rzeczywistym - na czym polega?
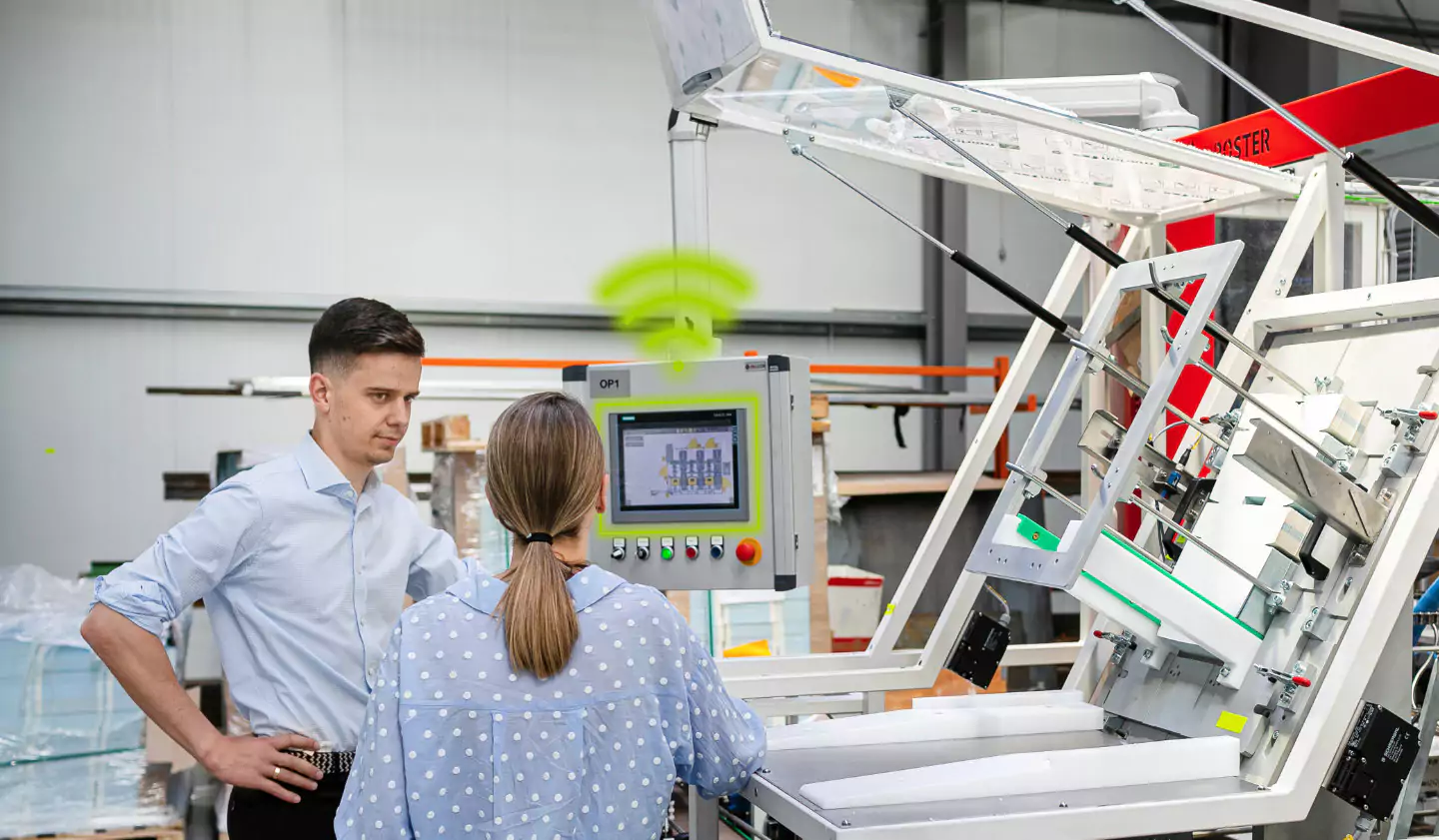
Ten artykuł jest dla Ciebie, jeżeli chcesz dowiedzieć się:
- Jak pozyskiwanie danych produkcyjnych wpływa na rozwój firmy,
- Co jest potrzebne do monitorowania produkcji w czasie rzeczywistym,
- Jak wygląda konkretny przypadek integracji produkcji z systemem ERP.
Monitorowanie produkcji jest pozyskiwaniem różnorodnych danych z produkcji, w celu zwiększenia efektywności procesów, a także dążenia do ciągłej optymalizacji produkcji. Można do tego zagadnienia podejść w sposób „tradycyjny” i zbierać dane ręcznie, a następnie ręcznie tworzyć raporty i analizować informacje. Można również podążać za tzw. przemysłem 4.0 i pozostać konkurencyjnym na rynku, wdrażając w swojej firmie rozwiązania pozwalające na automatyczny przepływ danych pomiędzy urządzeniami, maszynami, czy systemami zarządzania. Pozwala to nie tylko na wyciąganie szybszych wniosków o stanie produkcji na podstawie danych (przecież dzięki temu nie tracimy czasu na ręczne pozyskiwanie informacji i ich synchronizację), ale również na działanie z wyprzedzeniem, przewidywanie przestojów, automatyczne nadawanie wydajności, weryfikację jakości produktów i procesów kilkoma kliknięciami. Idąc dalej na automatyzację w dostępie do danych dla personelu operacyjnego.
Raportowanie i analiza produkcji, czyli jakie dane śledzić i w jaki sposób?
Im wcześniej uzyskamy informacje, tym szybciej będziemy w stanie zareagować na anomalie. Dlatego pozyskiwanie zintegrowanych danych w czasie rzeczywistym, z różnych urządzeń pozwala na oszczędność (przede wszystkim czasu i kosztów) zyskaną przez eliminację pracy z wieloma urządzeniami lub chociażby zdobycie danych od osób za to odpowiedzialnych. Jak pozyskiwać dane z procesów produkcyjnych?
Dane produkcyjne pozyskujemy bezpośrednio z maszyn i urządzeń, które są wyposażone we wbudowane systemy raportujące zbierane dane dotyczące wydajności, jakości, parametrów technicznych i innych istotnych wskaźników produkcyjnych. Przykładami takich systemów do monitorowania są SCADA, MES, PLM, czy MRP. Dane do tych systemów są pobierane bezpośrednio z programowalnych sterowników logicznych (PLC) i czujników, które pozwalają na monitorowanie stanu urządzeń, ilości wytworzonych jednostek czy czasach cyklu. W wielu procesach produkcyjnych stosuje się etykiety z kodami kreskowymi, kodami QR lub technologią RFID (wykorzystanie fal radiowych do transportowania danych). Pracownicy lub urządzenia skanują kody podczas przemieszczania się produktów przez różne etapy produkcji.
Znamy już popularne metody pozyskiwania danych z zakładu produkcyjnego, a jakie parametry możemy mierzyć i gromadzić?
- rzeczywisty czas pracy maszyn oraz personelu,
- wydajność maszyn i urządzeń (np. wskaźnik OEE),
- zużycie narzędzi, maszyn i urządzeń,
- ilość przestojów, ich przyczyny oraz czas trwania,
- ilość wadliwych wyrobów i ich przyczyny,
- czasy cyklów produkcyjnych,
- stany magazynowe.
W czasach przemysłu 4.0 istnieją zaawansowane sposoby pozyskiwania informacji o urządzeniach. Jednak dane same w sobie nie dają wiele, jeśli nie są przeanalizowane, a następnie wyciągnięte odpowiednie wnioski. Ostatecznie cały ten proces pomaga podjąć kluczowe decyzje i wprowadzić odpowiednie usprawnienia w produkcji.
IoT w przemyśle – wyższy poziom monitorowania produkcji
IIoT, czyli Przemysłowy Internet Rzeczy (Industrial Internet of Things) jest koncepcją, która umożliwia lepszy przepływ danych pomiędzy urządzeniami, maszynami i całymi liniami produkcyjnymi, a systemami zarządzania produkcją. Zastosowanie bezprzewodowych czujników wibracji, temperatury, czy wilgotności, pozwala nie tylko na w/w korzyść, ale także na zapobieganie wielu usterkom i awariom. Celem jest znacznie bardziej szczegółowy monitoring produkcji, umożliwiający szybkie reakcje na zmieniające się potrzeby produkcyjne. Dzięki dynamicznemu rozwojowi zaawansowanych technologii, jak przetwarzania danych w chmurze, analizy dużych zbiorów danych (Big Data) lub sztucznej inteligencji (AI), jesteśmy w stanie stworzyć taki system monitorowania, który zapewni niespotykaną do tej pory kontrolę jakości realizacji produkcji.
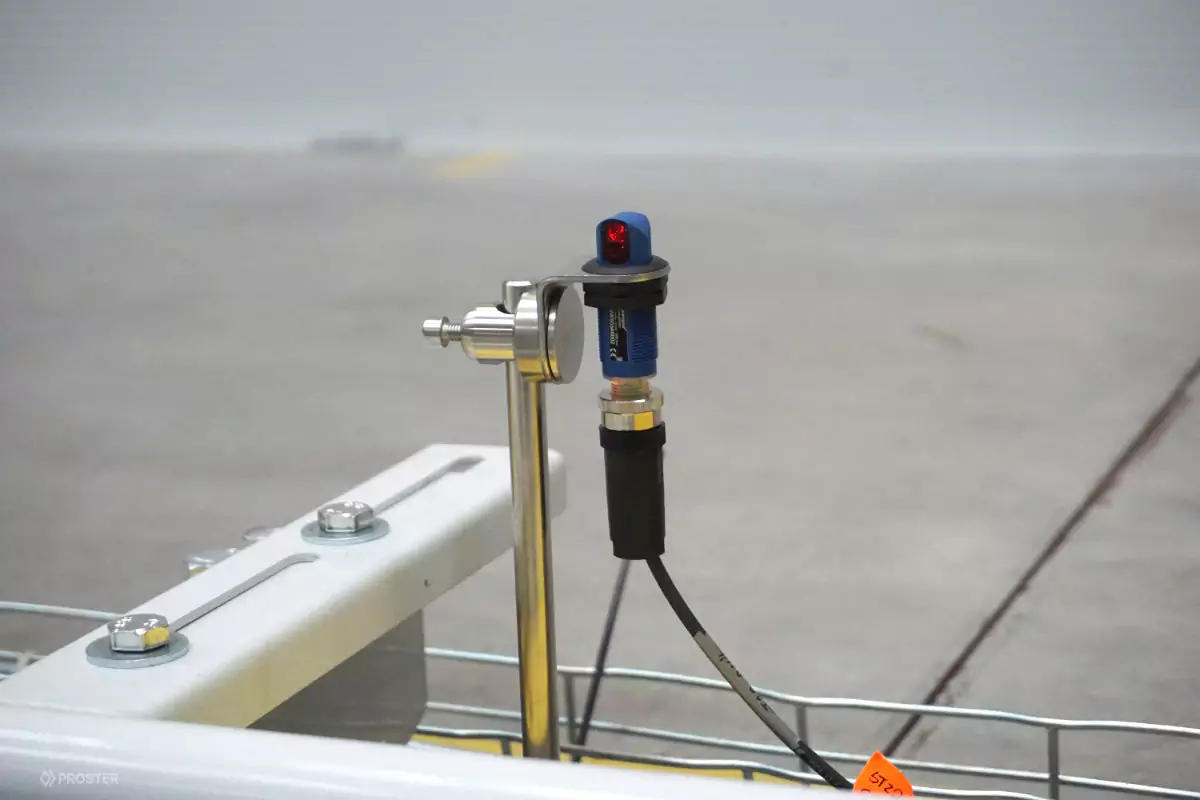
Integracja maszyn i urządzeń produkcyjnych z systemem ERP
Integracja ERP z produkcją to proces łączenia i synchronizowania procesów produkcyjnych z systemami zarządzania zasobami i produkcją przedsiębiorstwa. Celem tej integracji jest kompleksowe monitorowanie produkcji w czasie rzeczywistym, głównie na poziomie operacyjno-zarządczym organizacji. ERP bowiem, zbiera odpowiednio przygotowane dane z różnych systemów produkcyjnych, takich jak MES, SCADA, CMMS, WMS, czy MRP, a nawet ze sterowników PLC. Posiadając aktualne dane na temat wydajności, jakości wyrobów, stanu zapasów czy zamówień klientów, możemy zweryfikować wykonanie planu produkcyjnego, lepiej zrozumieć proces produkcyjny i dążyć do ciągłej jego optymalizacji. Ponadto dane te są przesyłane do reszty organizacji, co pozwala na upłynnienie wglądu w informacje w całej firmie.
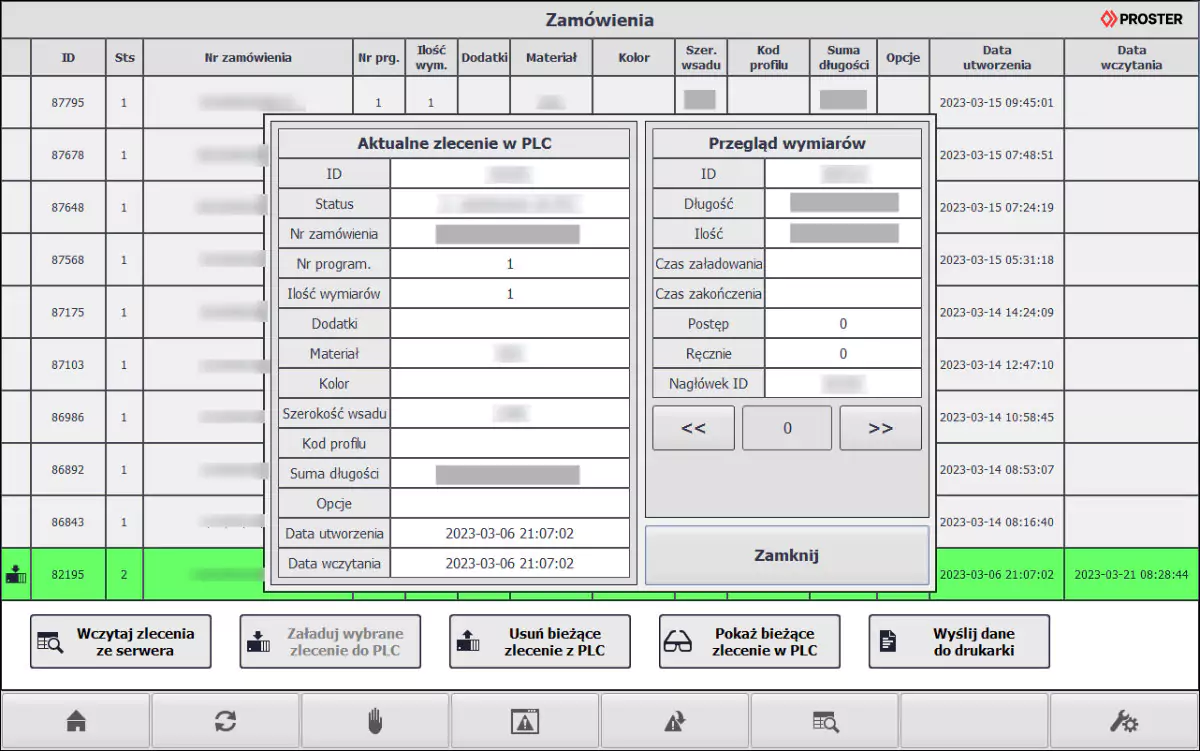
Widok panelu HMI zintegrowanego z zamówieniami, wysyłanymi do ERP
Główne korzyści z integracji systemów zarządzania z produkcją
- Automatyzacja wielu procesów, co prowadzi do ograniczenia ilości pracy manualnej i zmniejszenia ryzyka błędów,
- Działy zarządzania i kontroli w przedsiębiorstwie posiadają aktualne informacje produkcyjno-logistyczne, co ułatwia podejmowanie decyzji i planowanie,
- Śledzenie stanu magazynowego, sprawniejsze zamawianie brakujących surowców oraz optymalizację poziomu zapasów,
- W przypadku zmian w zamówieniach, harmonogramach produkcji lub dostępności surowców, integracja danych umożliwia szybką reakcję na te zmiany i dostosowanie procesów,
- Szybkie identyfikowanie i naprawianie problemów produkcyjnych, co przekłada się na poprawę jakości produktów i zwiększenie efektywności produkcji.
Dzięki monitorowaniu produkcji, przy pomocy dedykowanych systemów zarządzania, przedsiębiorstwa mogą osiągnąć lepszą kontrolę nad procesami produkcyjnymi, zoptymalizować koszty, zwiększyć wydajność i reagować szybko na zmiany rynkowe, co przyczynia się do zwiększenia konkurencyjności firmy na rynku.
Należy jednak pamiętać, że taka integracja wymaga kompleksowego podejścia do analizy procesów produkcyjnych, bez czego wnioski wyciągane z pozyskiwanych danych mogą być niedokładne.
W naszych artykułach edukujemy, aby decyzja o cyfryzacji zakładu produkcyjnego była świadoma i przemyślana. Jeśli chciałbyś to docenić, to zapoznaj się z naszymi usługami oraz realizacjami.