Wzrost wydajności paletyzacji oraz depaletyzacji owoców i warzyw dla Amplus
Projekt
Amplus jest rodzinną firmą produkującą i dystrybuującą owoce i warzywa na półki polskich sklepów. Firma zatrudnia prawie pół tysiąca pracowników, a w 2021 roku osiągnęła przychód ponad 1 miliarda PLN.
Robotyzacja procesu paletyzacji i depaletyzacji dla naszego partnera zakładała kompleksowo – doradztwo, projekt, montaż i uruchomienie linii, a także szkolenia personelu, integrację z systemem zarządzania i rozbudowę o automatyczną owijarkę palet. Najważniejszymi wyzwaniami, jakie wiązały się z tym projektem były:
- Projekt specjalnego chwytaka, dostosowanego do produktu
- Niski transport palet
- Szeroka gama referencji kartonów
- Połączenie procesu depaletyzacji i paletyzacji
- Wysoka wydajność linii
- Komunikacja z systemem nadrzędnym
- Owinięcie folią stretch palety (z zachowaniem wysokiego dostępu powietrza do owoców i warzyw)
Celem pracy linii było zmniejszenie ilości warstw kartonów na palecie (depaletyzacja), przy jednoczesnej paletyzacji produktu ze ściąganych warstw. Robotyzacja tych procesów pozwala na redukcję ręcznego przekładania ciężkich kartonów o wadze do 20kg, co wpływa na ograniczenie problemów zdrowotnych personelu. Ponadto usprawnia dystrybucję palet do klientów naszego partnera.
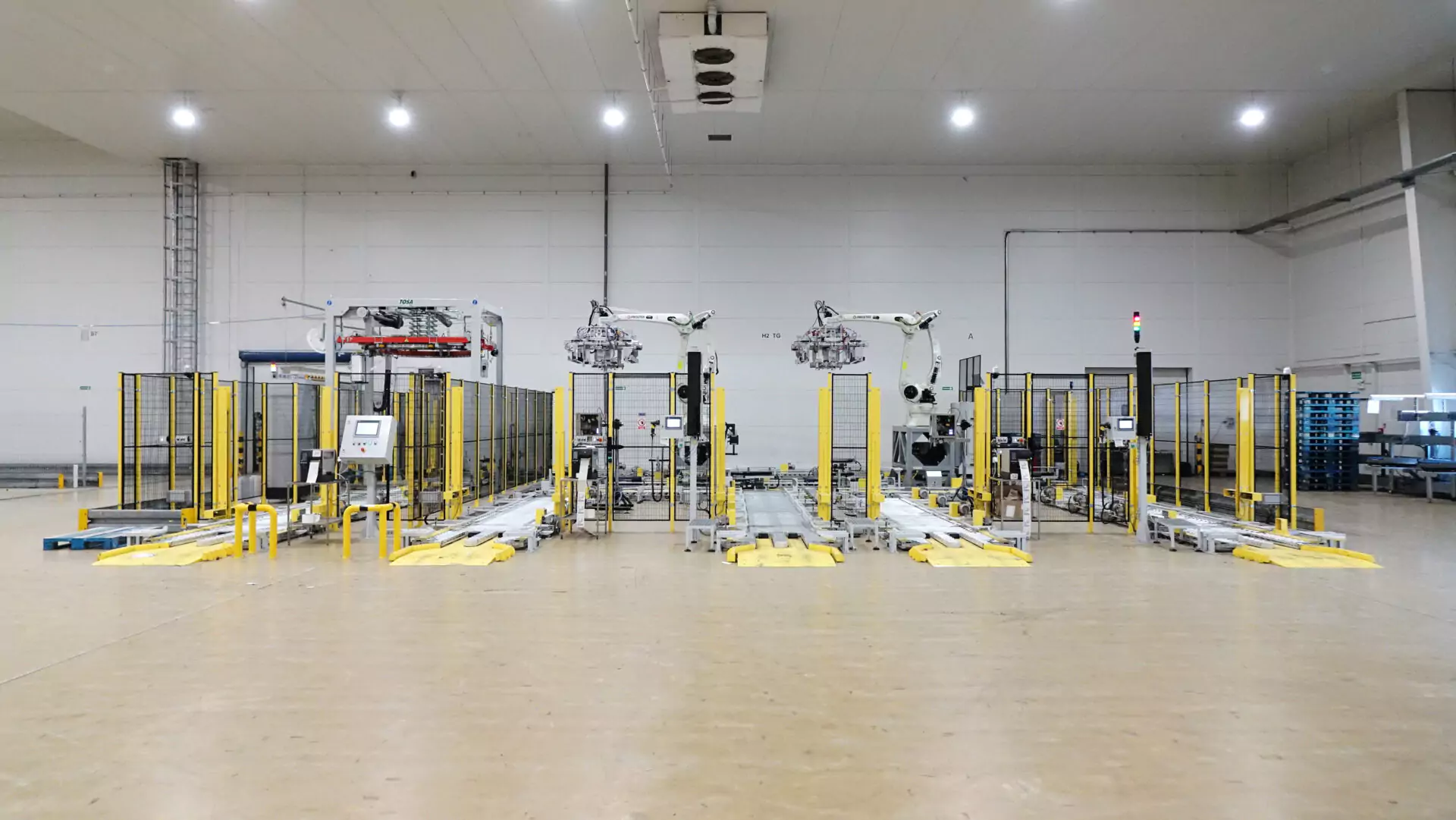
Opis linii paletyzacji i depaletyzacji
Procesy wewnątrz linii odbywają się w pełni automatycznie. Procedura depaletyzacji oraz paletyzacji rozpoczyna się w momencie pojawienia się palet na odpowiednich przenośnikach. Nowo ułożone palety kierowane są do automatycznej owijarki do palet, skąd transportowane są do odbioru.
Strefy wprowadzenia palety
Proces depaletyzacji odbywa się w dwóch strefach, zaprojektowanych modułowo. W sekcji wprowadzenia palety z produktem, operator rozpakowuje paletę do wymaganej wysokości, oznaczonej za pomocą znacznika LEDowego, stojącego obok wjazdu na linię. Następnie skanuje etykietę zbiorczą produktu. Dzięki temu, przekazywane są informacje o wprowadzanym produkcie do robota oraz etykieciarki, co skutkuje dostosowaniem odpowiedniego programu pracy robota i druku etykiet. Po umieszczeniu palet na przenośnikach wejściowych, operator potwierdza gotowość do pracy linii za pomocą przycisku na kasecie sterującej. Strefa wprowadzenia palety jest miejscem, w którym palety są kontrolowane pod względem jakości oraz przygotowywane do dekompletacji.
Strefy depaletyzacji i paletyzacji
Wjazd na strefę odbywa się w sposób automatyczny, na przenośnikach rolkowych i obrotnicach. Jedna strefa depaletyzacji pozwala na zbuforowanie na przenośnikach od jednej do pięciu palet.
Linia została zaprojektowana w taki sposób, aby depaletyzowany produkt został automatycznie umieszczony na nowej palecie (paletyzowany).
Nowe palety są wydawane przez automatyczny magazyn, który jest w stanie przechowywać do 12 sztuk, a następnie pojedynczo wydawać je do linii, w odpowiedzi na zapotrzebowanie zgłoszone przez system sterowania.
Strefa owijania palety i odbioru
Stosy gotowych palet z produktem, po zakończonym procesie paletyzacji, transportowane są układem przenośników i obrotnic do owijarki, a po drodze automatycznie zostaje naklejona etykieta. Palety, dzięki automatycznemu owijaniu, są szybko i powtarzalnie zabezpieczone do dystrybucji dla klientów.
Obszar pracy całej linii zabezpieczony jest wygrodzeniem ochronnym. Strefy wejścia w obszar linii chronione są przez system kurtyn świetlnych z opcją mutingu. Dzięki temu zostają zachowane najwyższe standardy bezpieczeństwa tego typu rozwiązań.
Rozwiązania Proster
Najważniejszym etapem pracy naszego zespołu było zaprojektowanie i wdrożenie do produkcji chwytaka, który jest w stanie pobrać całą warstwę kartonów i odkładać je tworząc równe stosy. Kartony są otwarte od góry, co jest nietypowym opakowaniem dla tego typu automatyzacji i stanowiło niemałe wyzwanie. Tego typu opakowanie jest mniej stabilne od zamkniętych kartonów, a zawarte w nim owoce i warzywa, sprawiają, że staje się wilgotne, dodatkowo utrudniając proces. Ponadto takie opakowania zawierają ząbki pozycjonujące, poprawiające stabilność całej palety z produktem, ale zmuszające robota do pracy z niezwykłą precyzją.
Chwytak robota składa się z zespołu ruchomych band bocznych, które pozwalają na powtarzalne chwytanie pakietu kartonów oraz odpowiednie pozycjonowanie ich na nowej warstwie. Pozycje band bocznych regulowane są przy pomocy serwonapędu, który umożliwia płynne przezbrojenie chwytaka w zależności od referencji oraz regulację siły docisku kartonów. Dodatkową funkcją jest przenoszenie pustej palety do strefy paletyzacji.
Zespół transporterów i obrotnic został zaprojektowany specjalnie pod wymaganie partnera. Pozwalają one na transport palet na wysokości 100 mm od posadzki, dzięki czemu możliwe jest zastosowanie niskich wózków paletowych.
Następnie proces owijania palety folią stretch wymagał zaprojektowania specjalnego podnośnika, który umożliwia integrację z systemem niskich transporterów, bez konieczności ingerencji w posadzkę. Podnośnik jest w stanie unieść paletę o wadze do jednej tony o wysokość 80mm.
Użyte rozwiązania Proster:
- Chwytaki robotów 2 w 1 – do otwartych kartonów oraz palet
- Przenośniki rolkowe 100mm
- Obrotnice rolkowe 100mm
- Automatyczny magazyn palet
- Podnośnik do palet
- Sterowanie na Panelu HMI
Ponadto:
- Roboty Kawasaki do paletyzacji
- Owijarka do palet Tosa
- Etykieciarki
- Systemy bezpieczeństwa
Proces realizacji projektu
Posiadamy zespoły projektowe i realizacyjne z zakresów automatyki, robotyki, mechaniki, jak również elektryki (łącznie z prefabrykacją szaf sterowniczo-zasilających). Tak kompleksowe i jednocześnie zgrane zespoły, pozwalają na realizacje projektów linii produkcyjnych i technologicznych od początku do końca. Nie inaczej było w tym przypadku. Wszystkie prace zostały zrealizowane przez zespoły Proster, nadzorowane przez liderów i project managerów.
Jeszcze przed realizacją, dzięki doświadczeniu z tego typu rozwiązaniami, doradziliśmy partnerowi usprawnienia w procesach, które pomogą zoptymalizować działanie linii.
Etap konstrukcyjny zakładał między innymi zaprojektowanie chwytaka robota i specjalnych przenośników oraz obrotnic rolkowych. W międzyczasie odbywały się prace automatyków i robotyków, związane z zaprogramowaniem sterowania linii i robotów przemysłowych do pracy z produktem.
Po przeprowadzonych pracach konstrukcyjnych i montażu mechanicznym i elektrycznym poszczególnych urządzeń, przeprowadziliśmy testy linii oraz kluczowych elementów automatyki. Zbudowaliśmy nasz chwytak, który przetestowaliśmy pod względem wytrzymałościowym i wydajnościowym. Pozwoliło to na udoskonalenie go tak, aby wykorzystać w pełni jego funkcjonalność.
Testy w obecności partnera
Na naszej hali montażowej powstała skrócona wersja stanowiska, dzięki czemu mogliśmy na wczesnym etapie skonfigurować oraz przetestować programy sterowania. Pozwoliła ona również na przeprowadzenie testów funkcjonalności oraz wydajności linii, na których byli obecni przedstawiciele naszego partnera.
Po zaakceptowaniu testów, nastąpił montaż mechaniczny oraz elektryczny w zakładzie Amplus. Po uruchomieniu całej linii nasi programiści skupili się na optymalizacji i osiągnięciu pełnej wydajności pracy całego stanowiska.
Ostatnim etapem projektu było przeprowadzenie szkolenia z obsługi linii dla personelu Amplus, przekazanie linii partnerowi (wraz z instrukcją obsługi oraz konserwacji maszyn i urządzeń) oraz wsparcie z asystą produkcyjną.
Wyzwania
Kartony otwarte od góry są nietypowym produktem w automatycznej paletyzacji, który wymaga niezwykłej precyzji. Tego typu opakowanie jest mniej stabilne od zamkniętych kartonów, a zawarte w nim owoce i warzywa, sprawiają, że staje się wilgotne, dodatkowo utrudniając proces. Ponadto takie opakowania zawierają ząbki pozycjonujące, poprawiające stabilność całej palety z produktem, ale zmuszające robota do pracy z niezwykłą precyzją. Rozwiązaliśmy to wyzwanie, projektując dedykowany do tego produktu zaawansowany chwytak robota.
Innym wymaganiem było wprowadzenie palet za pomocą niskich wózków paletowych. Do tego celu zaprojektowaliśmy zespół transporterów i obrotnic na wysokości 100mm od posadzki.
240
palet / zmianę to średnia wydajność linii
Korzyści dla naszego partnera
Zaprojektowana oraz wykonana przez nas linia paletyzacji i depaletyzacji owoców i warzyw dostarczyła firmie Amplus wymierne korzyści
-
Automatyzacja procesów
odpowiada na wzrost zapotrzebowania produktów na rynku, podążanie za trendem przemysłu 4.0 i wzrost siły przerobowej
-
Wzrost wydajności procesu
dzięki robotom, które mogą pracować nawet 24/7
-
Ograniczenie problemów zdrowotnych personelu
dzięki redukcji ciężkiego przekładania kartonów o wadze do 20 kg
-
Kompleksowe przeszkolenie personelu
zapewnia bezpieczeństwo i higienę pracy podczas eksploatacji linii depaletyzacji
-
Instrukcje obsługi i konserwacji urządzeń
zapewniają bezpieczeństwo użytkowania i długą żywotność linii
-
Doradztwo w optymalizacji procesów
pomogło lepiej przygotować się do zmiany w zakładzie
-
Sprawniejsze przygotowanie do dystrybucji palet dla klientów
zapewnia większy spokój dla partnera i zadowolenie jego klientów
-
Większa powtarzalność owinięcia palety
jednocześnie zapewniająca odpowiednią cyrkulację powietrza i bezpieczeństwo w transporcie
-
Serwis gwarancyjny i pogwarancyjny PROSTER
gwarantuje szybką reakcję na telefon i spokój w razie awarii systemu
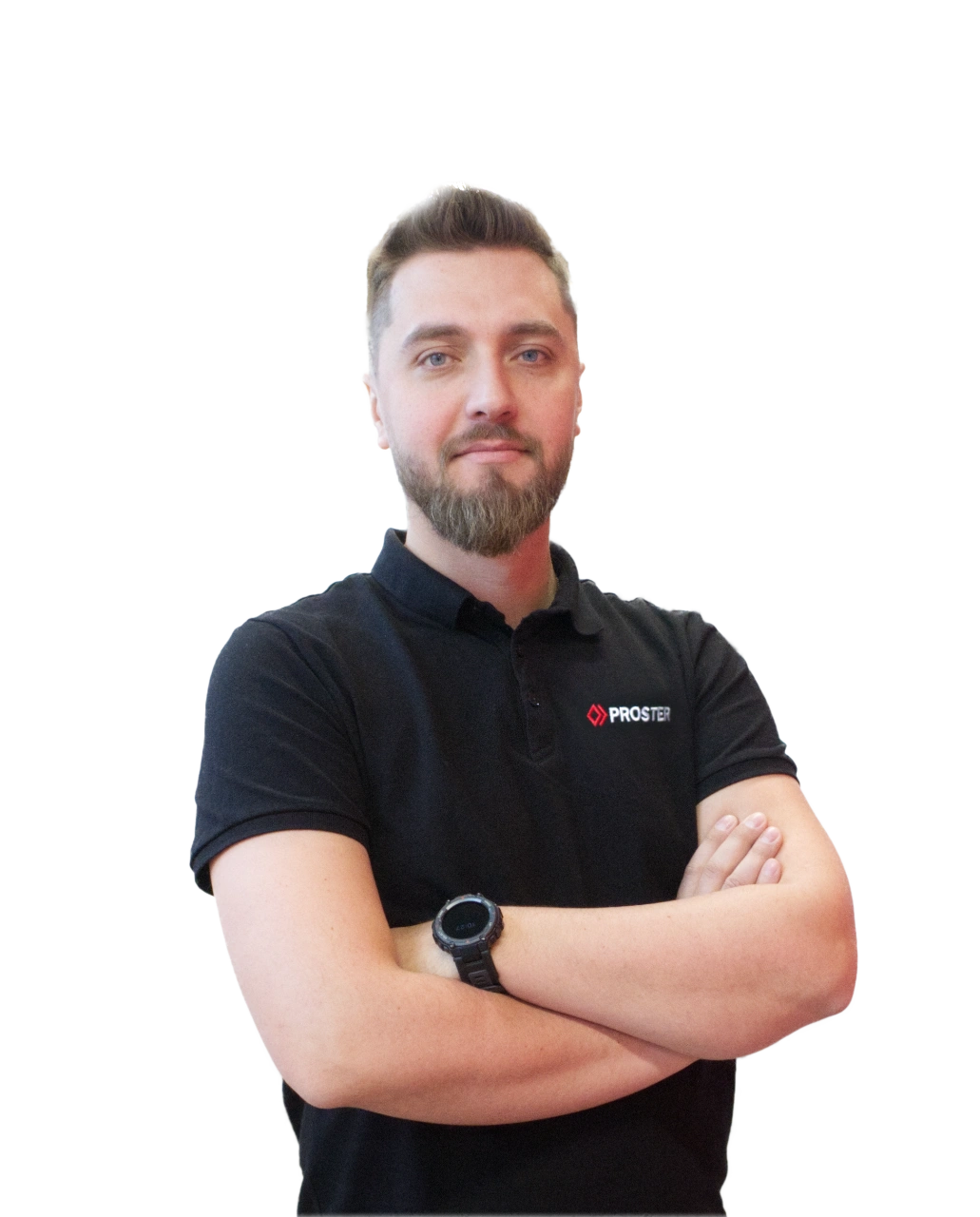
Porozmawiaj z doradcą
Wyślij zapytanie lub zadzwoń pod +48 513 221 627. Porozmawiamy kilka minut o wyzwaniach, które przed Tobą.