Artykuły Proster - źródła profesjonalnej wiedzy
Branżowa wiedza zebrana przez specjalistów dla specjalistów. Skorzystaj z doświadczenia naszych ekspertów.
Popraw wydajność produkcji dzięki robotyzacji
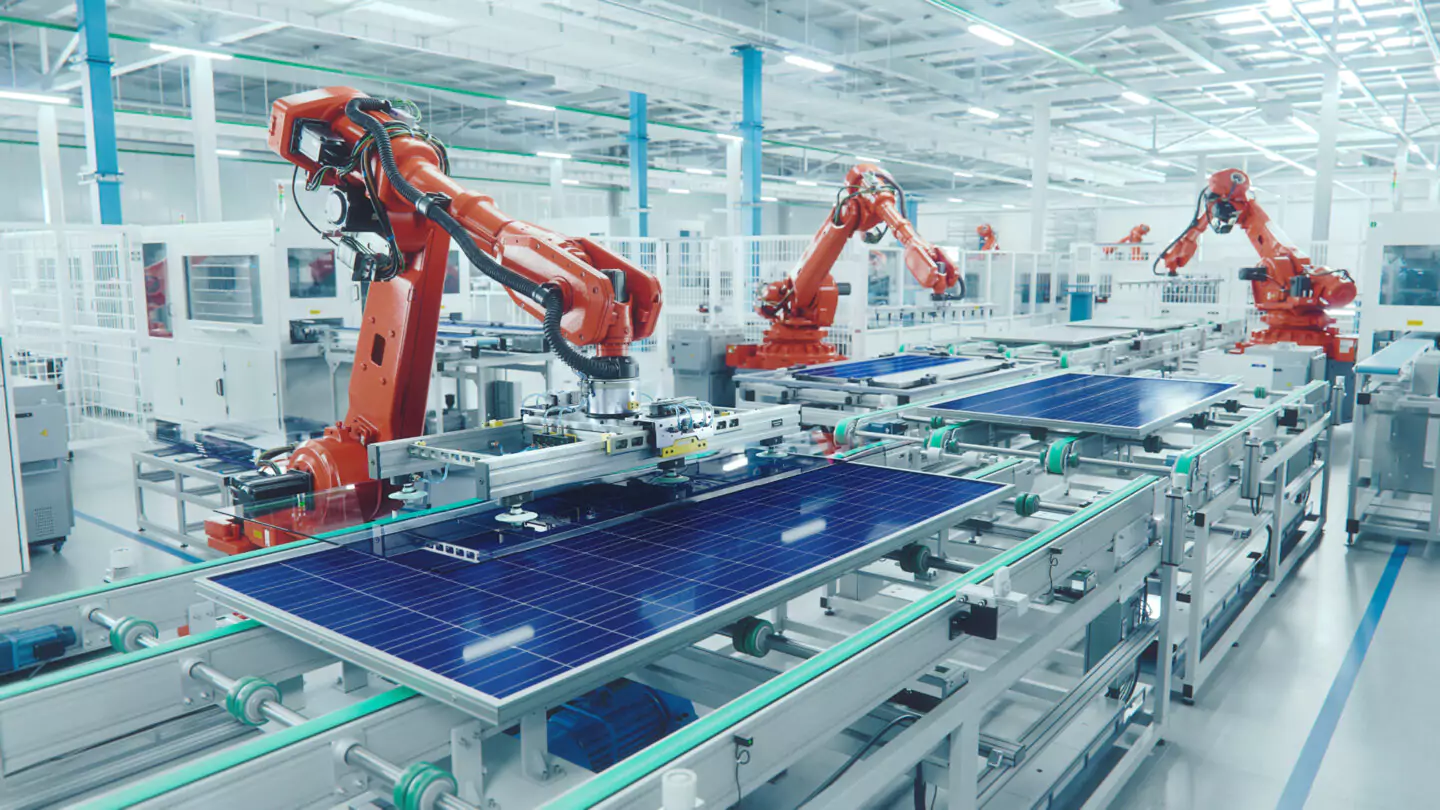
Ten artykuł jest dla Ciebie, jeśli:
- Chcesz zminimalizować uzależnienie produkcji od kompetencji pracowników,
- Chcesz skupić się na doskonaleniu produktu, a nie ciągłych problemach produkcyjnych,
- Chcesz dowiedzieć się jak skutecznie poprawić wydajność produkcji.
Poprawa wydajności produkcji to bezsprzecznie jedno z najważniejszych celów zakładów przemysłowych. To zadanie może być bardzo wymagające, ale tylko wtedy, gdy produkcja nie jest odpowiednio przygotowana do planowanych zmian. Dlatego, aby skutecznie i realnie zwiększyć moce przerobowe należy podjąć kroki, bez których zmiany będą jedynie krótkotrwałe i wykonywane bez większej świadomości. Czas, jaki zyskamy na rozwój produktów poprzez minimalizację problemów na produkcji jest bezcenny.
Należy zaznaczyć, że sposoby polepszenia wydajności produkcji różnią się dla każdego zakładu produkcyjnego. Zależą one bowiem od wielu czynników, jak etap rozwoju zakładu, poziom rozwoju technologicznego, ilość zatrudnianych pracowników, wdrożone techniki zbierania danych, wielkość zakładu i wiele innych. Dla mniejszego zakładu nie ma potrzeby bowiem wdrażać zaawansowanego systemu zarządzania produkcją, który dostarczy nam dziesiątki wskaźników. Co innego dla rozwiniętych zakładów, gdzie danych możliwych do uzyskania i miejsc optymalizacji może być znacznie więcej.
Zbieraj dane o swojej produkcji
Dla skutecznego doskonalenia produkcji istotne jest zbieranie odpowiednich danych, na których będziemy się opierać. W analizie procesów nie możemy polegać na naszych domysłach, a na twardych faktach. Najważniejszymi wskaźnikami, które należy mierzyć, aby określić miejsca do optymalizacji są między innymi czasy cyklów poszczególnych etapów produkcji, wskaźniki zużycia materiałów i wykorzystania maszyn, dane jakościowe nt. wadliwych wyrobów, odrzutów, czy reklamacji. Ważne są również czasy i ilości przestojów spowodowanych awariami lub nieprawidłowym użytkowaniem urządzeń, ponieważ zwracają uwagę na wadliwość maszyn, ale także pozwalają ocenić sprawność działania utrzymania ruchu. Czas poświęcany na poszczególne zadania w każdym z procesów przydaje się np. do porównania wydajności pracowników. Mierzenie zapełniania buforów może jasno zwrócić uwagę na miejsca, gdzie występują wąskie gardła.
Jeśli nie jesteś w stanie odpowiedzieć na podstawowe pytania, należy zastanowić się nad wprowadzeniem metod, na podstawie których uzyskamy informacje potrzebne do udoskonalenia wydajności. Pracownicy mogą rejestrować dane w dziennikach produkcji, kartach czasu pracy, kartach kontroli jakości, czy innych raportach. Mogą również używać szablonów Excel do zapisywania danych, żeby uprościć ich dalsze przetwarzanie. Jednak, szczególnie dla większych zakładów, najlepiej wykorzystać zaawansowane systemy monitorowania produkcji jak MES lub ERP, które pozwalają automatycznie zbierać dane z różnych etapów procesu produkcyjnego. Dzięki nim w czasie rzeczywistym przeanalizujemy produkcję i sporządzimy raporty. Co więcej, stosując automatyzację zbierania danych, jak czujniki, systemy identyfikacji, systemy wizyjne ograniczymy błędy ludzkie i uzyskamy dokładne dane. W celu skutecznej identyfikacji wąskich gardeł należy zbierać co najmniej podstawowe informacje o procesach, którymi zarządzamy.
Zidentyfikuj wąskie gardła
Niska wydajność produkcji może prowadzić do strat finansowych i utraty klientów, ale zastosowanie narzędzi identyfikacyjnych może pomóc w wykryciu i rozwiązaniu problemów. Wąskie gardła są takimi miejscami w produkcji, w których przepływ materiałów, informacji lub zasobów jest ograniczony lub spowolniony. Niedoskonałości mogą występować w różnych obszarach, od właściwej produkcji, logistyki, zarządzania zapasami, nawet do obsługi klienta. Wykrycia wąskich gardeł można dokonać głównie poprzez:
- Analizę przepływu produkcji od momentu rozpoczęcia procesu, aż do dostarczenia gotowego produktu. Zidentyfikuj, które etapy mogą powodować opóźnienia w przepływie i skoncentruj się na tych obszarach, które są najbardziej krytyczne,
- Dokładne monitorowanie czasu cyklu dla poszczególnych etapów produkcji. Zwróć szczególną uwagę na procesy, które trwają zbyt długo, zapełniają bufory lub wręcz przeciwnie, gdzie występują braki w materiałach. Może pojawiają się anomalie, które zwrócą uwagę na potrzebę optymalizacji. Na przykład różnica w wydajności pracowników lub wydajności różnych zmian. Odpowiedz na pytania dlaczego tak się dzieje? Może maszyna jest zbyt przeciążona na drugiej zmianie lub najzwyczajniej w świecie pracownicy wymagają szkoleń podnoszących kwalifikacje.
- Wykorzystanie danych produkcyjnych pochodzących z raportów, jak wskaźniki wydajności, czy jakości, aby dokładnie przeanalizować procesy. Porównaj wyniki z ustalonymi celami.
- Analizę stanu zapasów i przepływu materiałów między procesami poprzez diagram spaghetti. Czy istnieją obszary, w których występuje przepełnienie buforów lub braki w materiałach?
- Obserwację produkcji bezpośrednio na miejscu. Zwróć uwagę na etapy, gdzie występują przestoje, zatory, brak synchronizacji między etapami produkcji, czy nadmiar personelu. Potencjalnie tam występują wąskie gardła.
To bardzo ogólne sposoby identyfikacji wąskich gardeł, lecz mają na celu zwrócenie uwagi na to, że bez popartego faktami określenia tych miejsc w produkcji, nie będzie możliwa poprawa jej wydajności skutecznie i długotrwale.
Sposoby zwiększania wydajności produkcji
Osiągnięcie wysokich wyniki wydajności możliwe jest tylko przez zastosowanie odpowiednich metod i narzędzi. Zwiększanie wydajności może być wyzwaniem, ale nie trzeba nikogo przekonywać, że warto podjąć to zadanie. Zwiększenie zysków i konkurencyjności, a także zmniejszenie przestojów i zyskanie czasu na rozwój produktów to korzyści, o których marzy każdy właściciel przedsiębiorstwa czy kierownik linii produkcyjnej. Jakim sposobom poprawy wydajności warto się przyjrzeć?
- Analiza i doskonalenie układu linii produkcyjnej może zmniejszyć odległości między stanowiskami pracy, zapewniając płynny przepływ materiałów i informacji. Do tego celu możemy użyć na przykład wspomnianego diagramu Spaghetti, który polega na obserwacji drogi jaką przemierza produkt od wprowadzenia do produkcji, aż do jego wykonania końcowego. Celem jest zoptymalizowanie trasy, aby zredukować niepotrzebne ruchy. Można go zastosować również do analizy pracowników. Sposobów analizy przepływu materiału w przedsiębiorstwie jest mnóstwo, a zaawansowanym sposobem na ich weryfikację jest symulacja komputerowa. Pozwala na wirtualne testowanie różnych scenariuszy i wariantów układu linii. Dzięki temu można ocenić wpływ zmian w układzie, zwiększenie wydajności maszyn, czy zmianę organizacji pracy.
- Inwestycja w rozwój pracowników poprawia ich efektywność i samodzielność, dzięki czemu sprawniej radzą sobie z problemami i stają się bardziej zaangażowani. Podnoszenie kompetencji oprócz redukcji błędów przez lepsze przygotowanie do wykonywanych zadań sprawia, że pracownicy rozwijają się zawodowo, zyskując większy zapał do pracy. Poza tym ambitniejszy personel może przenieść skuteczne dla przedsiębiorstwa metody optymalizacji ze szkoleń do produkcji. Zwiększa to poczucie sprawczości u pracowników, a zakładowi daje wykwalifikowanego i samodzielnego pracownika.
- Systematyczne monitorowanie i analiza danych dostarczają cennych informacji na temat efektywności procesów, identyfikacji wąskich gardeł i możliwości optymalizacji. Dane dotyczące wydajności, jakości, czasu cyklu, zużycia półproduktów, itp. pomagają w podejmowaniu świadomych decyzji. Dla ciągłego doskonalenia regularne zbieranie i analiza danych jest konieczne. Dodatkowo pozwala na śledzenie postępów i ocenę skuteczności wprowadzanych zmian.
- Automatyzacja wprowadza innowacyjne technologie poprawiające szybkość wykonywanych czynności, co bezpośrednio przekłada się na poprawę rzeczywistej wydajności produkcji. Monitorowanie nowych trendów, technologii i rozwiązań branżowych oraz świadome wdrażanie tych zmian pozwala także na utrzymanie konkurencyjności i nadążanie za rynkiem. Robotyzacja nie jest jedynie modnym trendem, ale obecnie jednym z najlepszych sposobów na zwiększenie wydajności przy jednoczesnej redukcji szeregu problemów występujących w wielu zakładach produkcyjnych. Przyjrzyjmy się szczególnie tej metodzie, która w ostatnim czasie zyskuje na popularności nie bez przyczyny.
Robotyzacja sposobem na zwiększenie wydajności produkcji
Robotyzacja produkcji jest jednym z najnowocześniejszych sposobów na zwiększenie wydajności produkcji. W dzisiejszych czasach ten proces jest nie tylko coraz bardziej popularny, ale również niezbędny, jeśli chcemy konkurować na rynku. Dzięki zastosowaniu robotów, można „za jednym zamachem” zoptymalizować wiele procesów produkcyjnych i tym samym zwiększyć konkurencyjność firmy.
Jak robotyzacja wpływa na wydajność produkcji?
Przede wszystkim robot znacznie szybciej i precyzyjniej wykonuje swoje zadania, a więc zwiększa tempo produkcji, skracając czas cyklu. Pozwala na wytwarzanie produktu lepszej jakości, dzięki eliminacji błędów spowodowanych m.in. zwykłym zmęczeniem personelu. Roboty przemysłowe mogą pracować bez przerw, nawet przez 24 godziny na dobę. Odpowiednia synchronizacja z innymi procesami skraca czas przerw między nimi. Zrobotyzowane systemy są łatwo skalowalne i można je sprawnie dostosować do zmieniających się potrzeb produkcyjnych.
Robotyzacja może być wykorzystywana w różnych powtarzalnych procesach, a najbardziej powszechnymi są montaż, pakowanie i paletyzacja oraz depaletyzacja. Przy montażu i pakowaniu szczególnie istotna jest utrata koncentracji człowieka w trakcie wielogodzinnej pracy. Powoduje to wspomniane już błędy i utraty jakości produktu. W paletyzacji natomiast problemem jest monotonne przenoszenie ciężkich przedmiotów, które powodować może kontuzje pracowników. Nierzadko pracownicy odpowiedzialni z ten proces nie wykonują go przez całą zmianę, lecz muszą zmieniać się z osobami zajmującymi się czynnościami mniej obciążającymi. Do robota potrzebujemy jedynie operatora, który zostaje przeszkolony przez firmę wdrażającą rozwiązanie, a w przypadku konieczności serwisu integrator powinien zapewnić naprawę gwarancyjną lub pogwarancyjną, aby nie zostawić klienta z rozwiązaniem. Poza standardowymi procesami, roboty przemysłowe wykorzystywane są również do spawania, malowania czy nawet kontroli jakości, dzięki zastosowaniu systemów wizyjnych i czujników. To jedynie najbardziej powszechne czynności, a możliwości są szerokie i zależą od branży oraz potrzeb przedsiębiorstwa produkcyjnego.
Korzyści wynikające z zastosowania robotów przemysłowych w produkcji
Mimo, że polska produkcja zaczyna dostrzegać w robotyzacji szansę na rozwój, to nadal wiele firm nie jest przekonanych czy taka inwestycja rzeczywiście przynosi korzyści. A tych jest wiele:
- Wspomniane już zwiększenie wydajności produkcji,
- Poprawa jakości i precyzji. Zaprogramowanie robotów sprawia, że wykonują one wymagane czynności z tą samą dokładnością, co daje powtarzalność niemożliwą do uzyskania przez człowieka. Przekłada się to na jakość produktów, a pracownicy mogą być oddelegowani do procesów produkcyjnych, które są mniej monotonne i niekiedy obciążające fizycznie,
- Odpowiednio zaprojektowane systemy zrobotyzowane są stosunkowo łatwe w rozwoju i skalowaniu. Modularne projektowanie umożliwia proste wdrożenie kolejnych robotów skalujących wydajność procesu, a dostępność robotów przemysłowych w Polsce wzrasta, co przekłada się na szybki dostęp do systemów około stanowiskowych, jak czujniki, systemy wizyjne, przenośniki, etykieciarki, owijarki, czy systemy bezpieczeństwa.
- Roboty mogą być zintegrowane w linii produkcyjnej w sposób, który zapewni płynny przepływ materiałów, eliminując opóźnienia czy przestoje wynikające z błędów ludzkich. Dodatkowo integracja stanowisk zrobotyzowanych z systemem zarządzania produkcją (ERP) jest prosta i pozwala na jej monitorowanie oraz bardziej świadomą optymalizację,
- Zwiększenie bezpieczeństwa pracowników. Roboty mogą przenosić ciężkie przedmioty eliminując ryzyko urazów i wypadków, jakie może odnieść człowiek przy takich czynnościach. Posiadają zaawansowane systemy bezpieczeństwa, czujniki, wygrodzenia, czy strefy sterowania oddzielone od robotów. Poza tym roboty mogą pracować z toksycznymi substancjami co ogranicza ryzyko problemów zdrowotnych pracowników.
- Redukcja kosztów operacyjnych. Początkowo może się wydawać, że inwestycja w roboty przemysłowe może być kosztowna i w wielu przypadkach rzeczywiście tak jest. Długoterminowo jednak nie ma obecnie lepszego sposobu na tak znaczącą poprawę wydajności produkcji. Nieprzerwana praca robotów minimalizuje koszty produkcji związane z wynagrodzeniem, czy wdrażaniem nowych pracowników,
- Minimalizacja problemów z zatrudnieniem pracowników. Według raportu ManpowerGroup “Niedobór talentów”, aż 45% firm branży produkcji przemysłowej ma problemy z obsadzeniem etatów pracownikami produkcyjnymi. Robotyzacja może być odpowiedzią na ten problem, a dzięki atrakcyjnemu środowisku pracy istnieje większa szansa pozyskania pracowników o wyższych kompetencjach,
- Zyskanie czasu na rozwój produktu poprzez minimalizację problemów na produkcji.
Roboty przemysłowe mogą być także wykorzystane do wykonywania niebezpiecznych zadań, takich jak prace z substancjami toksycznymi czy wspomniane już manipulacje ciężkimi przedmiotami. Zmniejsza to ryzyka wypadków pracowników i poprawia warunki pracy. Dodatkowo posiadając roboty przemysłowe polepszamy wizerunek i atrakcyjność pracy w firmie nowoczesnej technologicznie.
W naszych artykułach edukujemy, aby decyzja o robotyzacji była świadoma i przemyślana. Jeśli chciałbyś to docenić, to zapoznaj się z innymi naszymi artykułami oraz usługami.