Zrobotyzowana depaletyzacja wełny mineralnej dla Ruukki
Projekt
Firma RUUKKI to firma z tradycjami, mająca swoje korzenie w Skandynawii. Jednym z oddziałów firmy jest zakład produkcyjny w Obornikach, w województwie wielkopolskim. W ramach działań mających na celu poszerzenie portfolio produkowanych płyt oraz zwiększenie wydajności i bezpieczeństwa na linii produkcyjnej, firma RUUKKI zdecydowała się na wprowadzenie nowego systemu zrobotyzowanej depaletyzacji arkuszy wełny mineralnej. Wśród wyzwań tego projektu znalazły się między innymi:
- wysoka wydajność linii depaletyzacji
- zapewnienie rozległego bufora rozładowywanych arkuszy
- możliwość jednoczesnej depaletyzacji różnych gatunków wełny mineralnej
- optymalizacja ilości rozładowywanych gatunków oraz miejsca depaletyzacji
- dostosowanie wydajności linii do bieżących potrzeb produkcji
- optymalizacja procesu wyboru gatunku wełny do depaletyzacji
- automatyczne monitorowanie transportowanych arkuszy i przekazywanie ich w odpowiednie miejsce
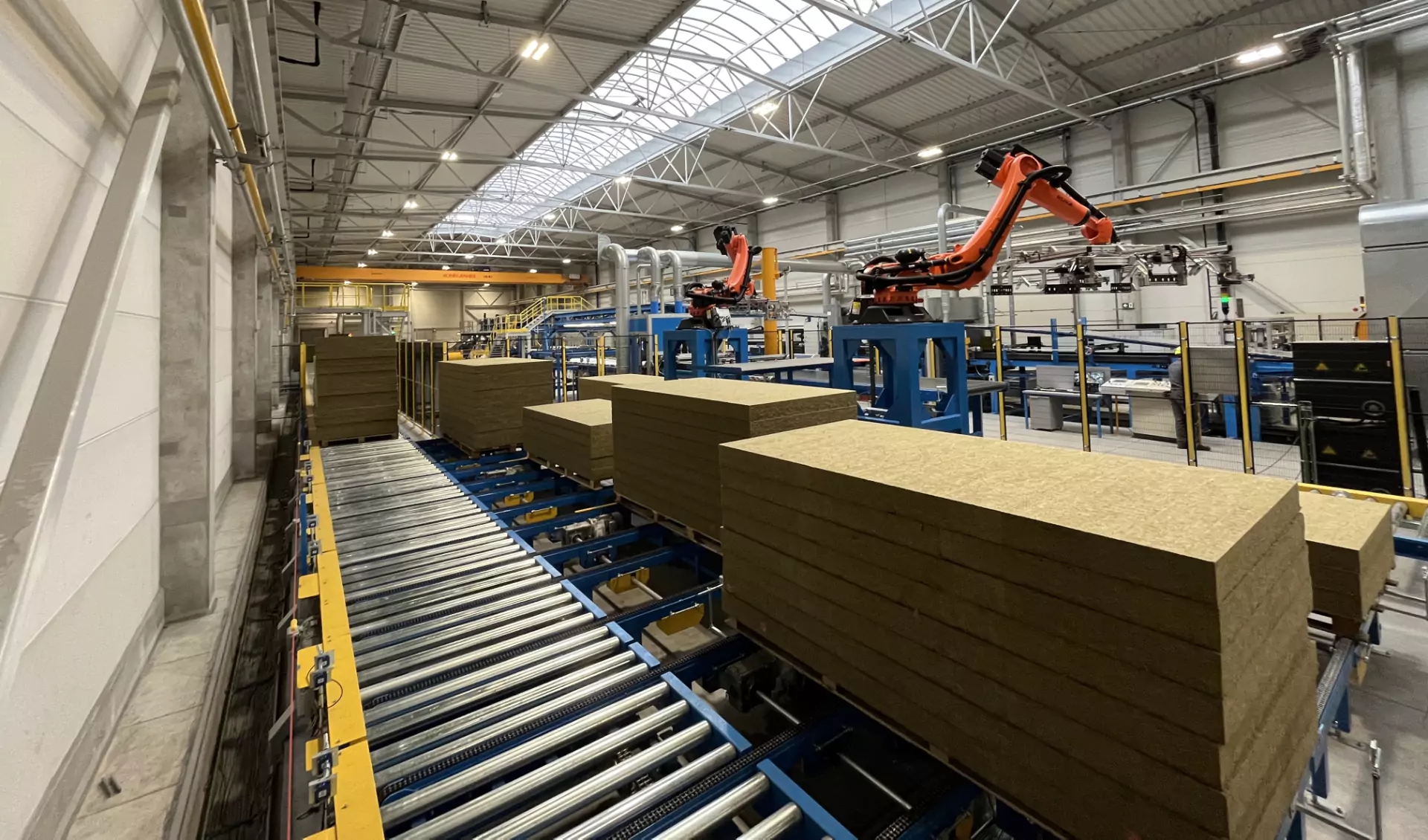
Rozwiązania Proster zastosowane w linii zrobotyzowanej depaletyzacji
Nową linię depaletyzacji zaprojektowaliśmy w taki sposób, aby oczekiwane zadania wykonywały dwa stanowiska z robotami. Było to konieczne, aby zapewnić zakładaną na początku projektu wydajność procesu.
Dostarczenie palet z arkuszami wełny mineralnej odbywa się poprzez zastosowanie przenośników rolkowych oraz łańcuchowych. Przenośniki rozlokowaliśmy na hali produkcyjnej w taki sposób, aby zapewniły rozległy bufor rozładowywanych arkuszy. W praktyce oznacza to nawet ilość 33 palet na przenośnikach (3 dostawy z tira).
Stosy palet na wejściu do zrobotyzowanych stanowisk są rozpakowywane ręcznie z folii ochronnej, a następnie transportowane do procesu depaletyzacji. Roboty zaprogramowaliśmy tak, aby miały możliwość niezależnego rozładunku arkuszy z czterech punktów poboru, co pozwala na zwiększenie wydajności procesu. Pobrany przez robota przemysłowego arkusz wełny jest odkładany na przenośnik taśmowy, który przenosi go do kolejnego etapu procesu technologicznego.
Zobacz jak zrealizowaliśmy ten projekt!👇
Użyte rozwiązania:
- Roboty Kuka do depaletyzacji
- Chwytaki robotów 2 w 1 – do arkuszy wełny oraz do palet
- System transportu wewnętrznego – przenośniki rolkowe i łańcuchowe
- Sterowanie na Panelu HMI
- Systemy bezpieczeństwa
Proces realizacji projektu
W okresie realizacji zaprojektowaliśmy kompleksowo zakres mechaniki, automatyki i robotyki, a także elektryki. Po czym wyprodukowaliśmy podzespoły mechaniczne i rozdzielnicę zasilająco-sterującą linią do depaletyzacji.
Proces realizacji rozpoczął się od zaprojektowania układu przenośników rolkowych, łańcuchowych oraz chwytaków do robotów. Następnie opracowany został projekt elektryczny oraz wykonanie rozdzielnic zasilająco-sterujących linią do depaletyzacji.
Jarosław Tynka, Senior Project Manager w Proster
Jednym z ważniejszych etapów pracy naszych inżynierów było zaprojektowanie i wytworzenie chwytaków mechanicznych dwuszczękowych. Posiadają one trzy główne funkcje: transport palet, transport arkuszy wełny mineralnej oraz transport pasków arkuszy. Każdą z tych funkcji, jak i między innymi konserwację mechanizmu napędowego chwytaków opisaliśmy szczegółowo w kompleksowej instrukcji obsługi linii.
Po etapie produkcyjnym przyszedł czas na testy stanowisk zrobotyzowanych na naszej hali montażowej przy udziale pracowników firmy Ruukki. Po akceptacji naszego rozwiązania zajęliśmy się transportem do zakładu w Obornikach, gdzie nastąpił montaż linii depaletyzacji.
Uruchomienie linii depaletyzacji
Po zakończeniu prac montażowych skonfigurowaliśmy urządzenia automatyki i samych robotów, a następnie testowo uruchomiliśmy naszą linię na różnych formatach półproduktu w postaci arkuszy i pasków wełny mineralnej – co przebiegło bez większych zakłóceń.
W pierwszej kolejności przeprowadziliśmy integrację linii depaletyzacji z linią produkcyjną klienta, gdzie skupiliśmy się na wymianie odpowiednich sygnałów pomiędzy nimi. Pozwoliło to skoordynować ich pracę tak, aby utrzymać warunek ciągłego podawania półproduktu w postaci arkuszy wełny mineralnej. Każda przerwa procesu depaletyzacji powoduje bowiem wstrzymanie ciągłej produkcji na linii wytwarzania płyt warstwowych, co wiąże się z kolei ze stratami czasu i materiału dla klienta.
Po dopracowaniu ciągłej depaletyzacji skupiliśmy się na osiągnięciu pełnej wydajności pracy linii z procesami produkcyjnymi. Na tym etapie były prowadzone głównie prace nad optymalizacją ruchów robotów, tak aby skrócić czas cyklu podawania arkuszy wełny mineralnej do minimum. Po kilku poprawkach w sekwencji pracy robotów udało się uzyskać oczekiwane rezultaty co do wydajności procesu zrobotyzowanej depaletyzacji. Ostatnimi etapami uruchomienia były szkolenia obsługi linii oraz służb utrzymania ruchu, a następnie przekazanie pod użytkowanie klienta z krótką asystą produkcyjną z naszej strony. Całość tych etapów trwała około dwóch miesięcy, po tym czasie klient mógł już w pełni użytkować zakupioną linę do depaletyzacji arkuszy wełny mineralnej.
100%
wzrostu wydajności procesu
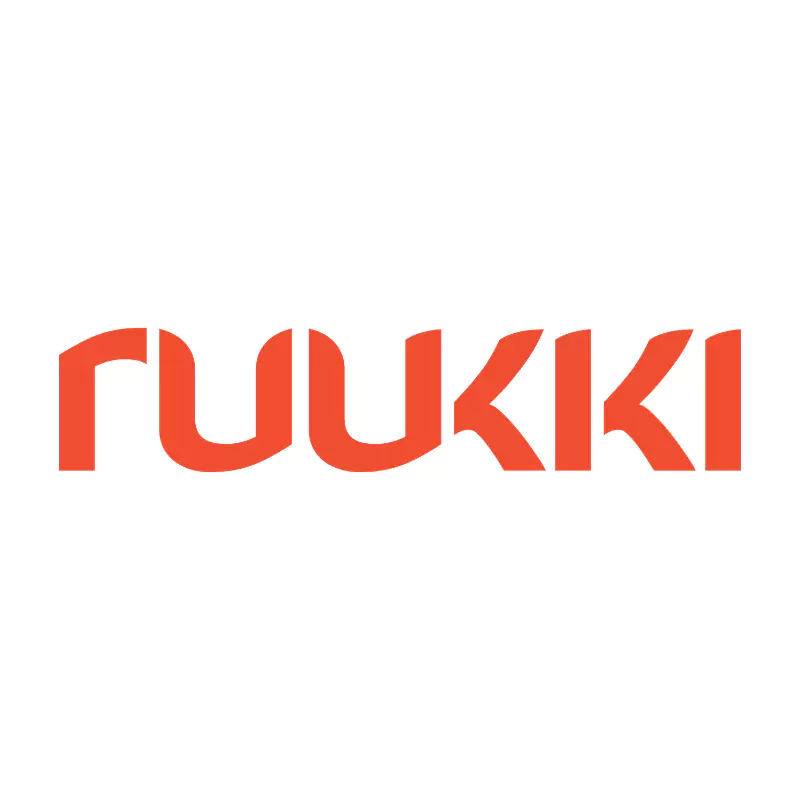
Powierzone prace zostały wykonane w pełni profesjonalnie i zgodnie z oczekiwaniami firmy Ruukki. Firma PROSTER charakteryzuje się rzetelnością i należytym zaangażowaniem w wykonywane prace. Zlecenie zostało zrealizowane sprawnie, dokładnie i terminowo. Polecamy firmę PROSTER jako wykonawcę kompetentnego i godnego zaufania, oferującego wysoką jakość usług.
Inżynier Procesu Ruukki Polska Sp.z.o.o.
Korzyści dla naszego partnera
Zaprojektowana oraz wykonana przez nas linia depaletyzacji arkuszy wełny mineralnej dostarczyła firmie Ruukki wymierne korzyści.
-
Wzrost wydajności linii o 100%
bezpośrednio wpływa na zwiększenie zysków przedsiębiorstwa
-
Wyższa efektywność
poprzez system umożliwiający śledzenie transportowanych arkuszy
-
Prostota przezbrojeń
umożliwia szybką zmianę rodzaju arkusza wełny, przy zminimalizowaniu przestoju linii produkcyjnej
-
Kompleksowe przeszkolenie personelu
zapewnia bezpieczeństwo i higienę pracy podczas eksploatacji linii depaletyzacji
-
Łatwe nadanie wydajności depaletyzacji
zwiększa kontrolę nad procesem produkcyjnym i optymalizuje wykorzystanie zasobów
-
Elastyczność procesu
dzięki funkcjonalności dostosowania do bieżących potrzeb produkcyjnych
-
Serwis gwarancyjny i pogwarancyjny PROSTER
gwarantuje szybką reakcję i spokój w razie awarii systemu
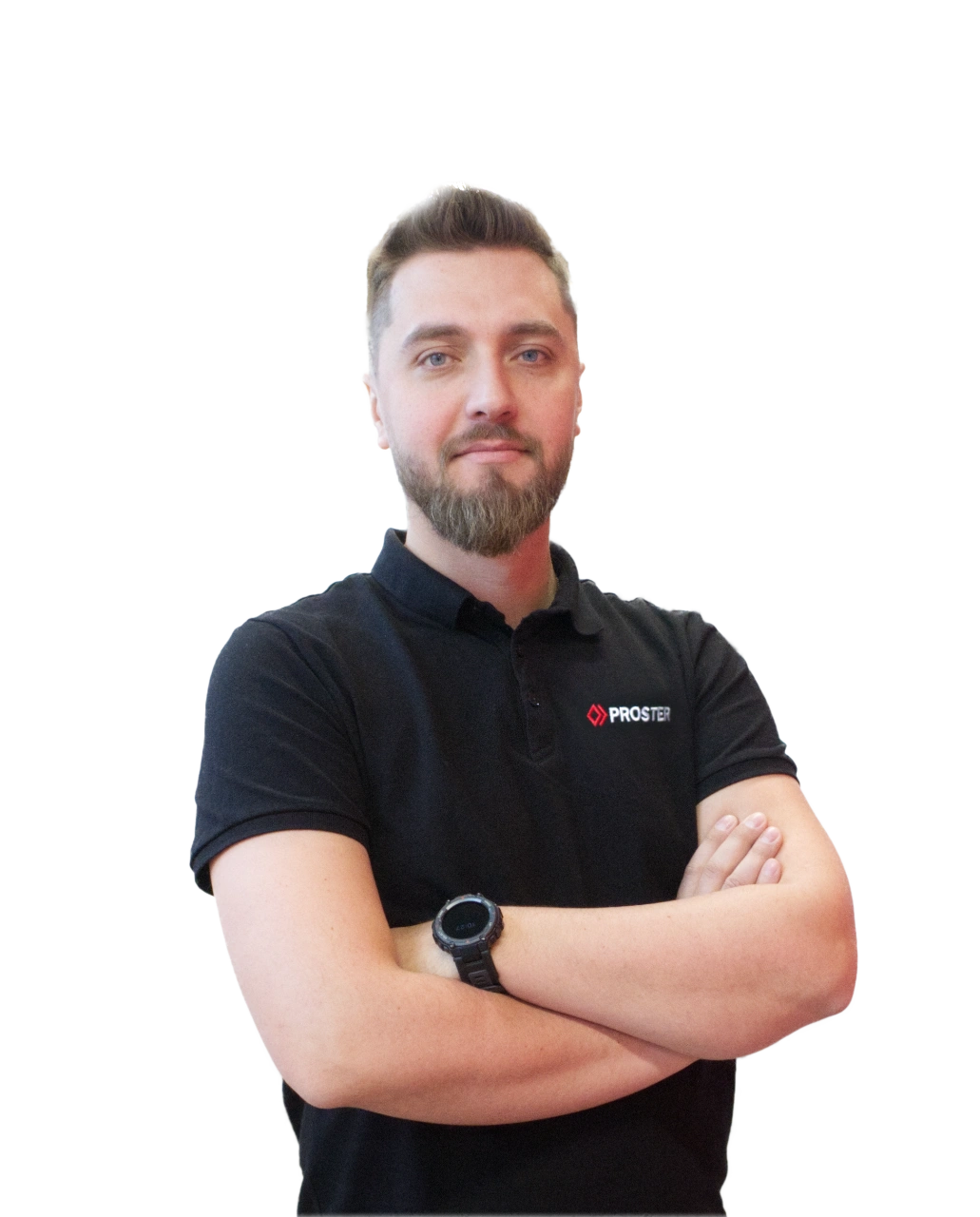
Porozmawiaj z doradcą
Wyślij zapytanie lub zadzwoń pod +48 513 221 627. Porozmawiamy kilka minut o wyzwaniach, które przed Tobą.