Modernizacja bramki jakości linii lakierniczej dla Baltic Wood
Projekt
Dla firmy Baltic Wood zmodernizowaliśmy bramkę jakości linii, której zadaniem jest separacja desek na deski zgodne, deski przeznaczone do odrzutu oraz deski przeznaczone do naprawy, na podstawie oceny wzrokowej operatorów pracujących przy linii.
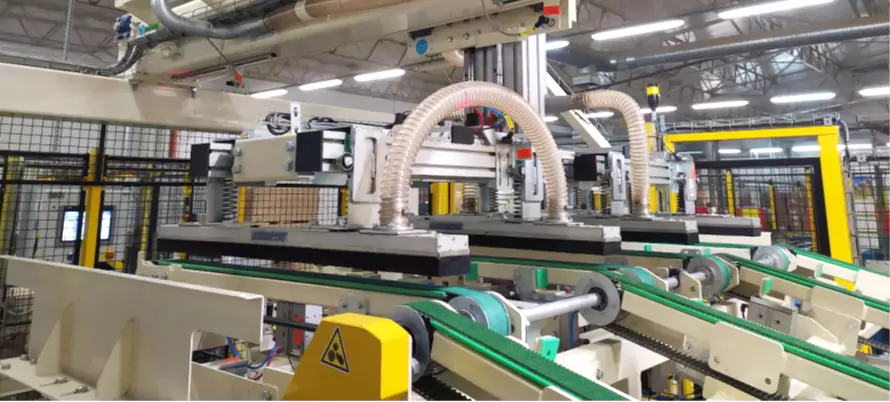
Segregacja i paletyzacja desek
Deski zostają załadowane na linię istniejącym manipulatorem linii lakierniczej na przenośnik [1], następnie załadowana warstwa desek jest przekazywana na przenośnik [2]. Z tego miejsca deski są wypuszczane pojedynczo, na przenośniku [3] odbywa się kontrola wizualna i tutaj obsługa decyduje czy deska jest bez wad czy z wadą.
Deski prawidłowe transportowane są przenośnikiem [4] na przenośnik [5], gdzie są układane w warstwy (szarże) do odbioru manipulatorem [6]. Manipulator paletyzujący pobiera warstwę desek i odkłada na przenośnik rolkowy [7] tworząc stos desek. Po ułożeniu wymaganego stosu desek zostają one przekazane po rolkach na przenośnik [8], gdzie czekają na odbiór wózkiem widłowym.
Deski z wadami są kierowane do magazynów [9] i [10], które są zamontowane pod przenośnikami pasowymi [4] i [5]. Zjazd desek do magazynów odbywa się poprzez uniesienie przenośnika [4] lub [5], a deska ześlizguje się do magazynu. W magazynach deski układane są w stos, który następnie jest spychany na przenośnik rolkowy [11] lub [12], a dalej rolkami wypychany na wózek [13]. Wózki służą do przewożenia stosu desek do innych stanowisk.
Realizacja projektu bramki jakości
Projekt mechaniczny i elektryczny
Do realizacji projektu wybraliśmy podejście klasyczne, mając podany zakres, termin oraz wynegocjowany budżet przystąpiliśmy do realizacji projektu tworząc zespół projektowy, który opracował najpierw konstrukcję mechaniczną współgrającą z zastosowanymi rozwiązaniami automatyki, następnie została opracowania część elektryczna projektu.
Produkcja urządzeń
Po realizacji etapu projektowego, zrealizowaniu zakupów i dostawie potrzebnych materiałów do projektu, przeszliśmy do realizacji produkcji zaprojektowanych urządzeń wchodzących w skład linii. Produkcja rozpoczęła się od procesów cięcia laserowego blach, a następnie ich formowania prasą krawędziową oraz lakierowania, a prawie równolegle powstawały elementy wykonane przez obróbkę skrawaniem. Wykonane i zakupione elementy zostały zmontowane w całość linii, która była gotowa do okablowania oraz uruchomienia wstępnego.
Prace elektryczne, programistyczne PLC oraz testy FAT
Przed wykonaniem okablowania linii, równolegle do produkcji mechanicznej została prefabrykowana i testowana rozdzielnica zasilająco-sterująca pracę linii oraz powstawało oprogramowanie do sterownika PLC i panelu dotykowego HMI. Po zakończeniu etapu montażowego, linia przeszła w etap uruchomienia testowego, podczas którego nasi inżynierowie automatycy testowali przygotowane wcześniej oprogramowanie, a także wprowadzali drobne usprawnienia. Całość uruchomienia wstępnego zakończyła się testami odbiorowymi w naszej siedzibie (FAT), podczas których przedstawicie klienta sprawdzili zgodność linii i realizowanej przez nią produkcji z założeniami przekazanymi na etapie ofertowania.
Transport i uruchomienie linii
Po przeprowadzonych z sukcesem testach FAT, linia została rozdzielona, spakowana do transportu, przewieziona i zamontowana w docelowej lokalizacji u klienta. Po tym etapie nastąpił etap finalnego uruchomienia produkcji na linii, w tym testów produkcyjnych z pełnym asortymentem produktów oraz pełnej wydajności linii. Całość została podsumowana testami końcowymi (SAT), po których obie strony podpisały protokół odbioru linii i linia przeszła do codziennego użytku w procesie produkcyjnym klienta.
Serwis gwarancyjny i pogwarancyjny
Nigdy nie zostawiamy klienta z rozwiązaniem. Oferujemy serwis gwarancyjny oraz pogwarancyjny, dzięki czemu klient może być spokojny w przypadkach awarii linii.
Korzyści dla naszego partnera
-
Ulepszona kontrola jakości produktu
pozwala realnie obniżyć koszty
-
Wzrost wydajności procesu
daje obniżenie czasu produkcji elementów
-
Minimalizacja ilości osób zaangażowanych w proces
pozwala przenieść zasoby ludzkie w inne miejsca procesu produkcji
-
Automatyczne przezbrajanie linii
oszczędza czas potrzebny na ten proces
-
Ocena jakości na wczesnym etapie
także obniża koszty w porównaniu do oceny jakości dopiero po uzyskaniu finalnego produktu
-
Serwis gwarancyjny i pogwarancyjny PROSTER
daje spokój w przypadku ewentualnych awarii na linii
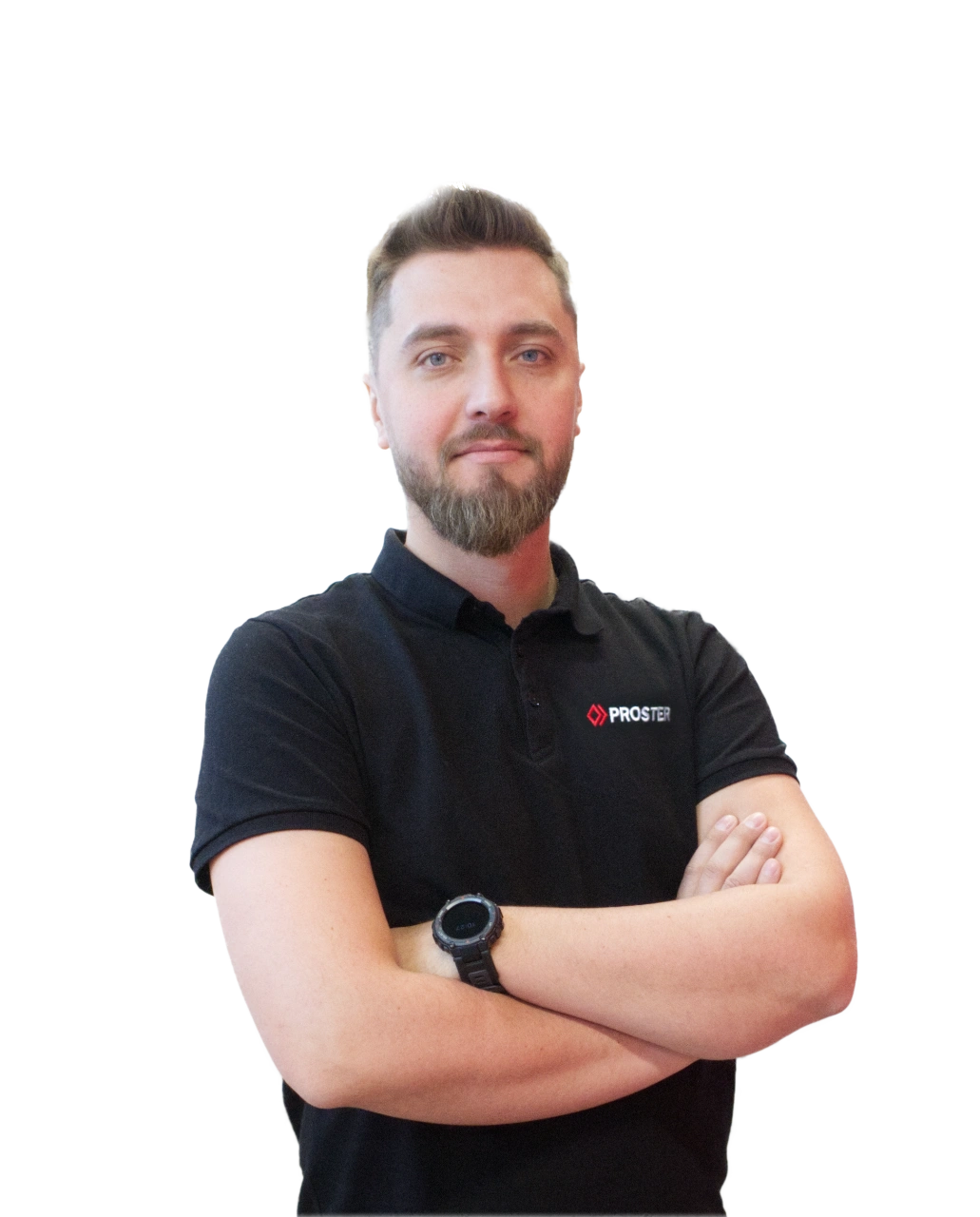
Porozmawiaj z doradcą
Wyślij zapytanie lub zadzwoń pod +48 513 221 627. Porozmawiamy kilka minut o wyzwaniach, które przed Tobą.